精益的意义——就设备维护和丰田生产方式(TPS)采访Harada先生(下)
本文是去年12月发布的《精益的意义——就设备维护和丰田生产方式(TPS)采访Harada先生》(点击这里阅读)一文的下半部分。在本文中,Tom Harada先生会更深入地与读者探讨不为人所知的丰田精益生产背后维护工作所起到的重要作用。相比欧洲国家,国内企业的设备可靠性和维护组织都相对薄弱,往往在发生安全生产事故后人们才刚开始认识到维护是阻碍企业精益生产的最大绊脚石。而启发和教育企业对维护的意识始终是喜科以及我们每月新闻通讯始终不变的主题。在此,要再次感谢Tom Harada和本文记者Art Smalley对我们的大力支持!
Art:
那丰田的维护组织架构究竟是怎样的呢?
那丰田的维护组织架构究竟是怎样的呢?
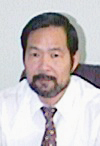
Tom:
这跟企业性质有关。在整车装配厂,由于生产线需连续不停运转,一旦发生故障,维护工程师的响应时间就显得至关重要。当然,这类工厂的设备一般并不复杂,因此需要在现场直接进行故障排除,而误差的范围应控制在毫米之间。通常这类工厂的维护组织会按照区域划分,维护技师有时需直接向生产经理进行汇报。
这跟企业性质有关。在整车装配厂,由于生产线需连续不停运转,一旦发生故障,维护工程师的响应时间就显得至关重要。当然,这类工厂的设备一般并不复杂,因此需要在现场直接进行故障排除,而误差的范围应控制在毫米之间。通常这类工厂的维护组织会按照区域划分,维护技师有时需直接向生产经理进行汇报。
而在发动机工厂,生产设备更为精密,可允许的误差值也必须控制在0.001毫米之内。因此我们需要花更多时间来培养精通电气、机械、液压、润滑、测量、模具等各方面的全能型维护人才。由此可见,这类工厂设备的平均修复时间要远远高于整车装配线。为此,我们专门配备了中央调度系统,并规定两人一组协同进行工作:一人会负责对故障情况进行诊断,而另一人则负责查看所需的图纸和备件等。通过这种教学相长方式不但工作效率更高,而且员工的技能也能得到很快的提升。
Art:
那维护与生产工人的人数比例在初级加工厂(如铸造、锻造、加工)与总装工厂之间是否存在差异?
那维护与生产工人的人数比例在初级加工厂(如铸造、锻造、加工)与总装工厂之间是否存在差异?
Tom:
那是当然。在设备密集型工厂,我们需要更多经验丰富、技能全面的工人,数量大概是普通工厂的2-3倍。在此我不想引用任何具体的数字,因为即使是同一工厂之间设备的生命周期也不尽相同。例如某加工车间正处于浴盆曲线底部的设备,其所需的维护资源当然要少于同处于浴盆曲线两端的设备。可以看出,这一数据不但不易获得,而且其参考价值也不是很大。此外,我们也会根据需要在工厂/车间之间调动所需的工程师。
那是当然。在设备密集型工厂,我们需要更多经验丰富、技能全面的工人,数量大概是普通工厂的2-3倍。在此我不想引用任何具体的数字,因为即使是同一工厂之间设备的生命周期也不尽相同。例如某加工车间正处于浴盆曲线底部的设备,其所需的维护资源当然要少于同处于浴盆曲线两端的设备。可以看出,这一数据不但不易获得,而且其参考价值也不是很大。此外,我们也会根据需要在工厂/车间之间调动所需的工程师。
Art:
你们所实施的维护工作分类哪几个类型?
你们所实施的维护工作分类哪几个类型?
Tom:
撇去各个工厂间的差异性不谈,就拿上乡的加工车间而言,一般我们至少有5种不同的基本维护工作类型:即故障维护(BM)、预防性维护(PM)、日常维护(DM)、预防性维护(CM)以及维护改进与预防(MP)。
撇去各个工厂间的差异性不谈,就拿上乡的加工车间而言,一般我们至少有5种不同的基本维护工作类型:即故障维护(BM)、预防性维护(PM)、日常维护(DM)、预防性维护(CM)以及维护改进与预防(MP)。
Art:
您可以就不同的维护种类做个简单的介绍吗?
您可以就不同的维护种类做个简单的介绍吗?
Tom:
BM(故障维护):由于牵涉到巨大的隐性成本,很显然我们希望能将花在BM以及其相关工作上的时间最小化,当然故障还是会发生,而我们也会竭尽所能地尽快对其进行处理。我们会研究故障问题并分析其修复所需的时间。此时SMED模型(9分钟即时换模)亦适用于维护工作,即所有简单的设备故障需在10分钟内解决。除此之外,我们也建立了详细的设备故障历史数据库,根据故障发生的频率和严重程度,重点关注和改进五大关键设备。
BM(故障维护):由于牵涉到巨大的隐性成本,很显然我们希望能将花在BM以及其相关工作上的时间最小化,当然故障还是会发生,而我们也会竭尽所能地尽快对其进行处理。我们会研究故障问题并分析其修复所需的时间。此时SMED模型(9分钟即时换模)亦适用于维护工作,即所有简单的设备故障需在10分钟内解决。除此之外,我们也建立了详细的设备故障历史数据库,根据故障发生的频率和严重程度,重点关注和改进五大关键设备。
PM(预防性维护)即为了防止故障的发生所开展的前期预防工作。我们拥有设备供应商提供的推荐PM列表,但我们也会根据设备实际情况及其生命周期对其行动方案进行补充。同时,我们也会调整PM的间隔和频率以防设备过度保养,从而造成不必要的资源浪费。
DM是由普通操作工(非熟练技工)开展的日常维护工作,包括简单的巡检和清洁工作,例如检查冷却剂消耗、刀具磨损、液压、油压等。通过这些例行检查,操作工可以发现许多细小的渗漏或损坏,从而工程师可以在交班时对其进行修理,防止较大故障的出现。
CM是纠正性维护(corrective maintenance)的缩写。在工厂中,设备经过几年的运转后或多或少都会出现一些问题。在权衡经济利益、投入产出以及对产品质量的影响后,我们会对设备的原始设计进行一定程度的改进。这类改进有时非常简单,例如改善夹具的设计或调整切割工艺。而如果某台设备长期出现反复性问题,凭借长期开展持续改进(kaizen)的经验,我们就会对其进行彻底的重新设计。
最后要说的就是维护改进——MP。在订购新设备时,资深工程师会在花很多时间来研究其后续的维护工作该如何进行。为避免日后不必要的投入,对设备最终规格的确认我们会抱着非常审慎的态度。随后,我们会测试设备并寻找简化维护工作的方法,如有需要,我们甚至会完全取消一些不必要的工序。这一技术含量极高的工作当然不会经常发生,一般只在设备使用期限达到10至15年时才会开展。
Art:
那在丰田维护工作的重点是什么?
那在丰田维护工作的重点是什么?
Tom:
这个问题很难回答,但我总结了一些丰田维护工作的要点:
这个问题很难回答,但我总结了一些丰田维护工作的要点:
首先,我们会仔细研究设备的生命周期,并在此基础上调整所需的资源,从而能高效率地开展维护工作以此保证设备运行的最佳水平。此外,我们也从来不会忽视或过度开展维护工作。
第二,我们非常注重维护工人的培训和技能的发展。在这个日新月异的时代,设备不断革新,为了赶上科技的脚步,我们必须去不停地完善自己。这不但包括技术等硬性技能,也包含个人素质等软性技能。我们会指导维护工程师如何利用标准实践来修理设备、解决问题并寻找故障根源,并同时发掘设备进行持续改善(kaizen)的需求。
第三,我们非常擅长基础数据的收集和趋势分析。在查阅历史数据库时,我能非常轻松地找到所有生产线所发生的全部故障,并能了解每一次故障的频率和影响程度。同时,我还可以根据设备、车间、故障种类等进行个性化筛选。这一切都要归功于我们对人员的培训,指导他们如何正确进行数据录入并理解其使用方法。这一点非常重要。
第四,我们十分注重维护工作的计划和具体执行。在设备运转时,生产部门不会允许我们花太多时间来研究其机械性能。针对那些关键设备,我们不得不在交班甚至周末时来开展工作。
第五,我们会妥善保管与维护相关的所有文档,从而辅助我们进行故障定义和分析。针对每台设备,我们都配有非常标准的文档体系并科学进行保管。这些文档包括PLC图纸、数控系统、备件列表、液压油/润滑油图标、设备装配图纸等。我们深知,没有这些技术文档我们根本无法开展工作。
最后,我们在维护组织中也开展持续改善(kaizen)工作。我们不但会列出每周/每月五大故障设备,还会统计维修时间并分析其用时过长的原因。对于某些经常出现问题的设备,我们会去咨询相关的外部供应商。而对于维修起来非常复杂的设备,我们会想法设法来简化其下一次工作的工序。对于可靠性问题,我们会与生产团队一起去寻求更好的生产流程。在日本,丰田与其设备供应商保持着非常紧密的合作关系,互相从对方身上吸取改进经验。
Art:
你们会计算OEE吗?
你们会计算OEE吗?
Tom:
OEE是一个很好的分析工具,但对丰田而言其参考价值并不大。从实际运用的角度来说,OEE有诸多的缺陷。用有6个数字相乘得出的数值来衡量企业所有设备的效率是一件非常危险的事,因为你无法判断75%的OEE与85%的OEE到底哪个更好。假设前者的结果是基于多样性生产线和较高的工具转换率,而后者的次品率则高达50%,单从数字上来说,你一时很难判别好坏。与其如此,还不如单独计算并分析独立的指标。同时,由于OEE并不与生产时间(或takt time)相关联,因此过分追求OEE还会可能会导致过度生产。而对于像上乡这类拥有5000人的大型工厂,如真的要计算OEE,那你就需要一支小部队去四处搜集所有所需的数据。因此,OEE对我们而言就是一个分析工具,而非管理参数。
OEE是一个很好的分析工具,但对丰田而言其参考价值并不大。从实际运用的角度来说,OEE有诸多的缺陷。用有6个数字相乘得出的数值来衡量企业所有设备的效率是一件非常危险的事,因为你无法判断75%的OEE与85%的OEE到底哪个更好。假设前者的结果是基于多样性生产线和较高的工具转换率,而后者的次品率则高达50%,单从数字上来说,你一时很难判别好坏。与其如此,还不如单独计算并分析独立的指标。同时,由于OEE并不与生产时间(或takt time)相关联,因此过分追求OEE还会可能会导致过度生产。而对于像上乡这类拥有5000人的大型工厂,如真的要计算OEE,那你就需要一支小部队去四处搜集所有所需的数据。因此,OEE对我们而言就是一个分析工具,而非管理参数。
Art:
综上所述,既然维护对于丰田的TPM来说如此重要,但为什么没有引起人们的关注呢?
综上所述,既然维护对于丰田的TPM来说如此重要,但为什么没有引起人们的关注呢?
Tom:
如果维护工作良好,设备运行正常,那生产团队势必会比维护团队得到更多的瞩目。而一旦出现问题,维护团队则会是首当其冲。这就是维护工作的特点,一般都扮演着默默无闻、幕后英雄的角色。单纯从TPM的理论出发,多数人认为只要精益做得好就根本需要维护。就如前文所说,任何去丰田或下乡进行考察的人都会被工厂执行精益的”盛况”蒙蔽了双眼,无法理解其实在精益背后,丰田在维护工作中所花费的大量精力和时间。
如果维护工作良好,设备运行正常,那生产团队势必会比维护团队得到更多的瞩目。而一旦出现问题,维护团队则会是首当其冲。这就是维护工作的特点,一般都扮演着默默无闻、幕后英雄的角色。单纯从TPM的理论出发,多数人认为只要精益做得好就根本需要维护。就如前文所说,任何去丰田或下乡进行考察的人都会被工厂执行精益的”盛况”蒙蔽了双眼,无法理解其实在精益背后,丰田在维护工作中所花费的大量精力和时间。
Art:
非常感谢您的合作!
非常感谢您的合作!