Aluminate cement group improves maintenance management at its oldest plant with CMMS
For more than a hundred years, Kerneos Aluminate Technologies (www.kerneos.com), has focused on supporting the development of its customers throughout the world. As an expert in calcium aluminate technology, the company offers high quality and innovative specialty products, often as a pioneer. Formerly known as Lafarge Aluminates, Kerneos is now part of Imerys Group.
Kerneos (China) Aluminate Technologies Co. Ltd, operates three special aluminate cement plants in Tianjin, Zhengzhou and Guiyang. In the past ten years, to comply with the Chinese government’s improved environmental standards and stricter safety inspections, Kerneos China top management has put forward higher requirements for the refinement of plant management. At the same time, with an expansion of production capacity in the various plants, Kerneos saw a rapid increase in maintenance costs caused by the gradual aging of equipment and continuous decline in reliability. Kerneos management team proposed the forward-looking plan to establish a maintenance information system to control all maintenance activities.
The Shawen plant was acquired by Kerneos and renamed Guiyang Jia Nai Special Aluminates. Due to the high capacity utilization and the traditional management model, the problem of equipment reliability had become increasingly prominent. The company identified a number of weak points:
1. Equipment documentation is incomplete and the equipment is not rated by criticality. SOPs are available only for the largest equipment. Preventive maintenance in general is very inefficient.
2. Although electronic documents exist for spare parts stock, the data is inaccurate and outdated. Critical spares, some of them with long delivery time and high cost, are not always available when needed.
3. Maintenance team workload utilization is unbalanced. Manpower plans related to maintenance activities for the various equipment are poor.
4. Repair and maintenance records are lacking. The plant uses paper work orders to record work, information recoded in Excel afterwards does not reflect the actual work. Extensive labor is required for data input.
5. The lack of data makes management decision-making difficult: discrepancies exist between data collected by different departments, financial figures deviate from warehouse and maintenance department records. Due to this low accuracy, only very broad management decisions can be made.
2. Although electronic documents exist for spare parts stock, the data is inaccurate and outdated. Critical spares, some of them with long delivery time and high cost, are not always available when needed.
3. Maintenance team workload utilization is unbalanced. Manpower plans related to maintenance activities for the various equipment are poor.
4. Repair and maintenance records are lacking. The plant uses paper work orders to record work, information recoded in Excel afterwards does not reflect the actual work. Extensive labor is required for data input.
5. The lack of data makes management decision-making difficult: discrepancies exist between data collected by different departments, financial figures deviate from warehouse and maintenance department records. Due to this low accuracy, only very broad management decisions can be made.
After careful consideration of the plant situation, extensive research and comparison of possible solutions, Kerneos decided to engage Siveco to implement the standardization requirements from Kerneos headquarters, to improve the Shawen plant equipment management, through the deployment of its CMMS Coswin.
Siveco China, founded in 2004, is a pioneer in the development of Smart Technologies for the Operation & Maintenance of infrastructures and industrial plants, with a focus on mobile solutions “for the worker of tomorrow”. Based on a long experience of “maintenance with Chinese characteristics”, the company has developed a unique approach combining expert maintenance consulting and innovative solutions designed in its Shanghai-based R&D center.
The project started in October, 2017 with a review of the plant situation and Kerneos headquarters requirements, followed by an initial training conducted by Siveco. The CMMS was fully operational 2 months later, going live in December, 2017.
The coding system and the architecture of the complete CMMS system are fully compliant with the “Common Language” defined by Kerneos Group, allowing easy benchmarking and information sharing between all plants: equipment types, classification and criticality are unified across all plants. Meanwhile, work classification and key performance indicators (such as corrective maintenance and preventive maintenance completion ratios) adopt the same standard worldwide, in order to maintain consistency when performing benchmarks.
In order to make the CMMS as easy-to-use as possible for production and maintenance personnel, the system’s user interface is entirely graphical, based on plant diagrams, ensuring smooth usage through the entire process from work request to work order completion. From the preliminary fault diagnosis (symptom input in the initial request) to the final root cause analysis (after repair) are recorded using systematic codes allowing statistical analysis. The plant manager and maintenance manager has visibility into which equipment type suffers most breakdown, through graphical reports.
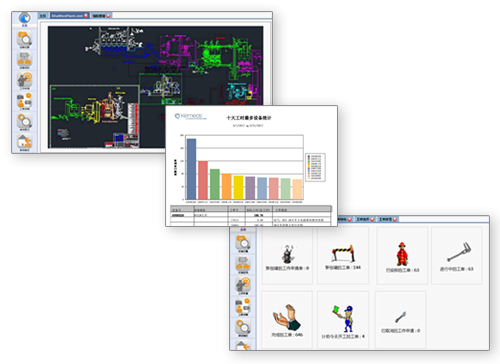
Adhering to the management concept that a proactive, preventive maintenance approach is better than a reactive approach, all key equipment of Kerneos (such as cement mill, kiln, etc.) are linked to predefined preventive work instructions in the CMMS (such as weekly/monthly/yearly maintenance SOPs). The system automatically proposes a maintenance plan, based on which mechanical and electrical planners can release work orders after verification with production schedules and approval of production. Finally, work is dispatched to specific staff whose skillset corresponds to the work order requirements. The maintenance supervisor or maintenance manager can also adjust the balance of the employees workload as needed.
According to Mr. Hu, China Maintenance Manager in Kerneos:
“This successful use of Coswin in Shawen plant proves that as long as the management team is dissatisfied with the status quo and has an enterprising spirit, even an older plant, organized for many years along traditional management principles, can greatly benefit from the support and management of experienced maintenance experts inside and outside the company, as well as the resolute execution of the local maintenance team and timely and accurate data maintenance, and ultimately benefit from a CMMS-driven improvement project.
We are very satisfied of the long-term working relationship with Siveco. I thank all members of the joint Kerneos-Siveco team for their great team work and look forward to continuous improvement thanks to the CMMS Coswin with yearly support from Siveco.”