Carrefour China over a decade: the natural evolution of a Risk Prevention system
In June 2011, Carrefour selected Siveco China to implement a nationwide Risk Prevention Management System (RPMS). The RPMS was based on Siveco China’s bluebee® suite of software solution, designed in compliance with the ISO 31000 Risk Management standard. The project implementation was described in this 2013 article. Siveco China and Carrefour won the 2013 CHaINA “Best Supply Chain Consulting Partner” Award by the Global Supply Chain Council, Asia’s leading professional organization in supply chain, for this project.
This short Customer story looks at how and why the RPMS evolved in the decade between 2011 and 2021, as a structuring, methodological and analytical tool to foster continuous improvement.
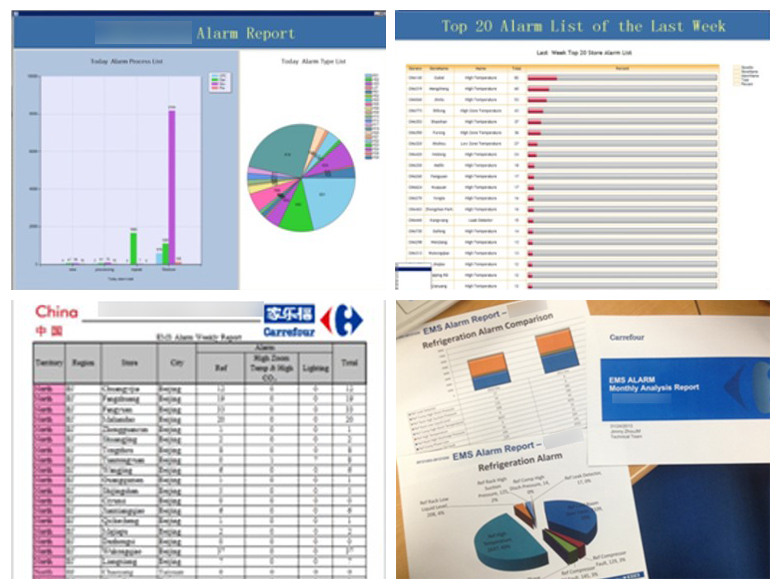
2010 – Before RPMS, the Carrefour Risk Prevention (RP) department used to work with paper, Excel sheets, all in the form of lists: list of incidents, list of control points, energy consumption records, etc. Graphical KPIs was compiled by hand in Excel, graphically improved in PowerPoint, to be finally printed and pasted on a display wall.
In the initial design of the RPMS, the managers expectation was for the system to reproduce such formats, both in terms of output (reports, display) but also input (end users screens). A consulting firm, appointed by the client to design such formats based on the existing practice, went as far as trying to design every screen of the system.
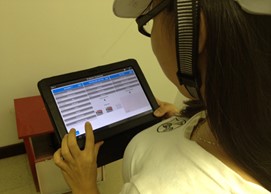
Siveco China’s focus turned to convincing Carrefour to switch to input methods that did not look like paper or Excel sheets, but instead would provide users with friendly step by step guidance, reduce workload and collect more accurate records. This led to the use bluebee® on mobile phones (for technicians) and on tablet (for risk auditors). And so was taken the very first true step on the path of improvement.
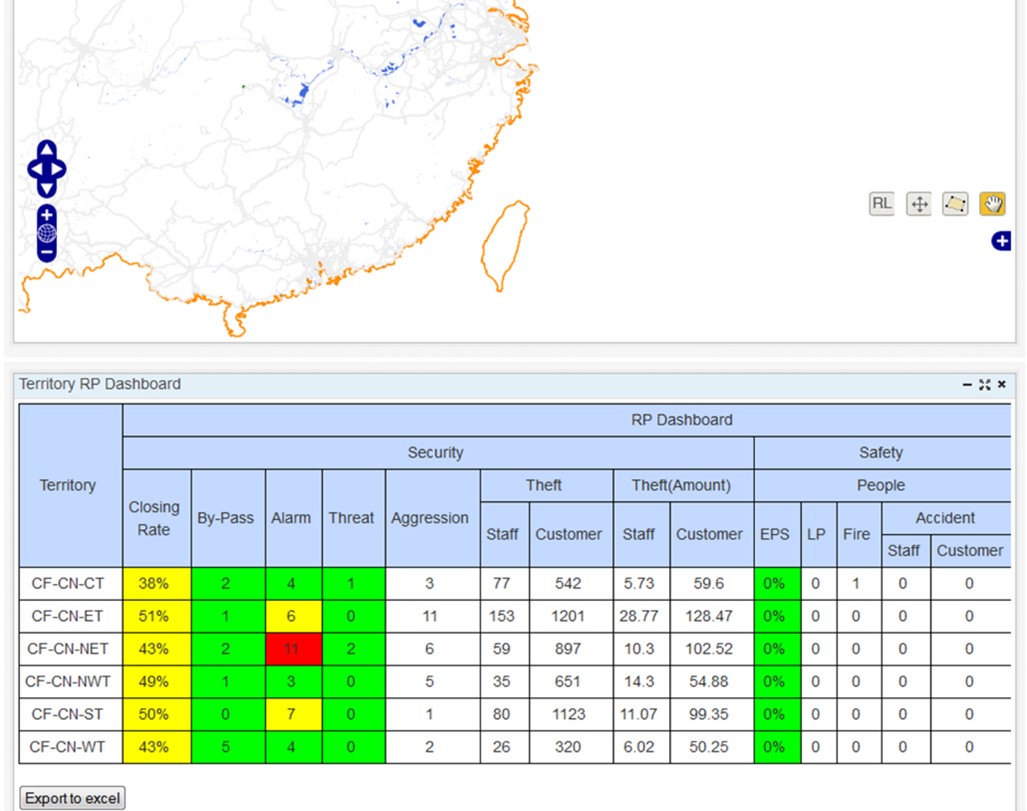
The output format, on the other hand, could not be changed. The initial reports in RPMS were thus designed to replicate Excel sheets (even though an export-to-Excel button is also available by default in the system). The only improvement that was accepted was that, depending on the status of the data, color would be added: green, yellow and red.
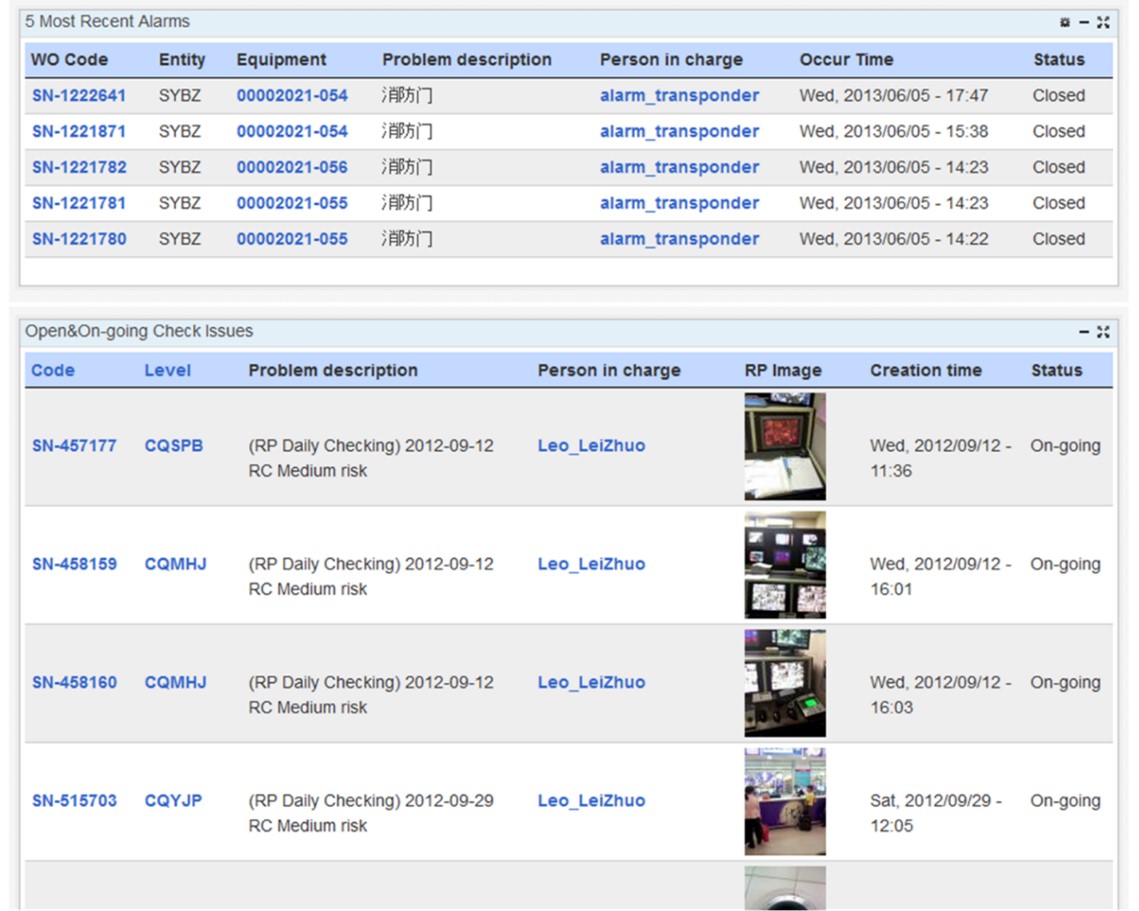
The RPMS also incorporated images directly in the records. All data including the photos came from actual records made on mobile devices by users on the bluebee® app.

Whenever the old paper format was required, the RPMS could automatically create a report in the old format. However, unlike the old manual system, all data remains in the system and can be traced, analyzed, audited.
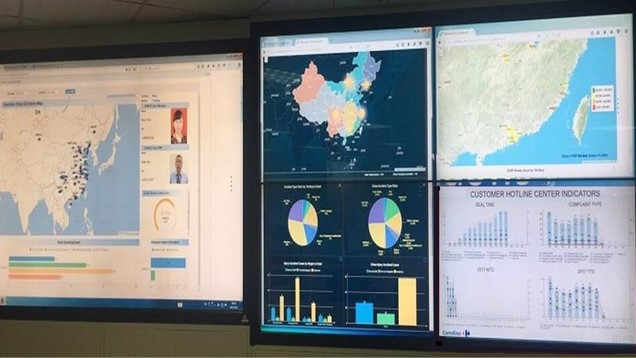
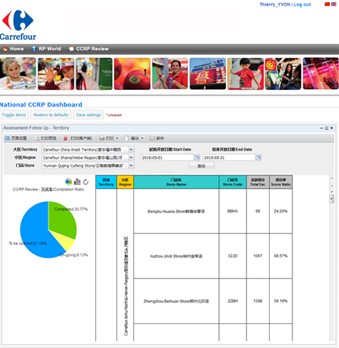
After a few weeks of using the RPMS and enjoying its benefits (see the original case study for that story), users and managers started to realize that instead of looking at long Excel-like screens with so many colors, they could just keep the yellow and red cases that required their attention! This lead to the realization that instead of showing lists, we could simply display pie charts and other graphics. Indeed, users do not need to be constantly looking at records, they could click as needed on the KPI if more information was needed, thus opening a specific record. Existing paper-KPIs on display were taken down and replaced by live charts in the RPMS itself.

As the RPMS proved its usefulness, the space dedicated to the system in Carrefour China’s COS center was expanded. Less useful systems moved into smaller screens, a large touch-screen display was added for the RPMS. Additional interfaces were created with various IoT systems to capture alarms, measurements, from hundreds of locations. More functionalities were added to the RPMS including technical maintenance.
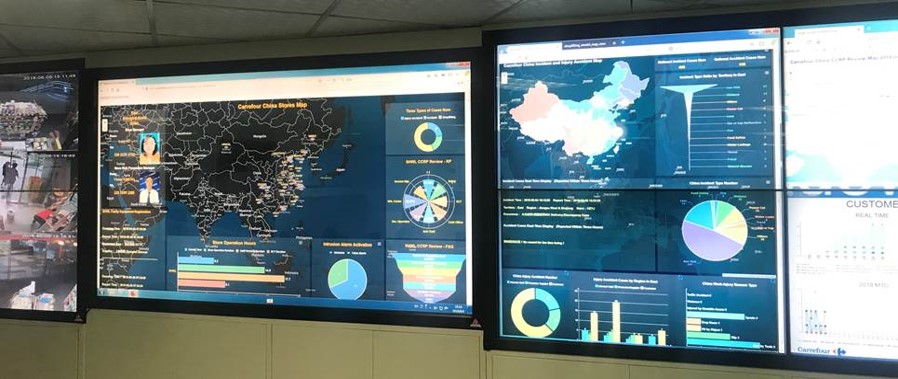
Around 2016, large screens had become commonplace in China and flashier displays on a dark background became fashionable. The RPMS had a more traditional white background display and more static charts. Carrefour China started to experiment and adopted a more modern outlook for the RPMS. A engineer was hired to take charge of the user interface and received training by the Siveco China team.
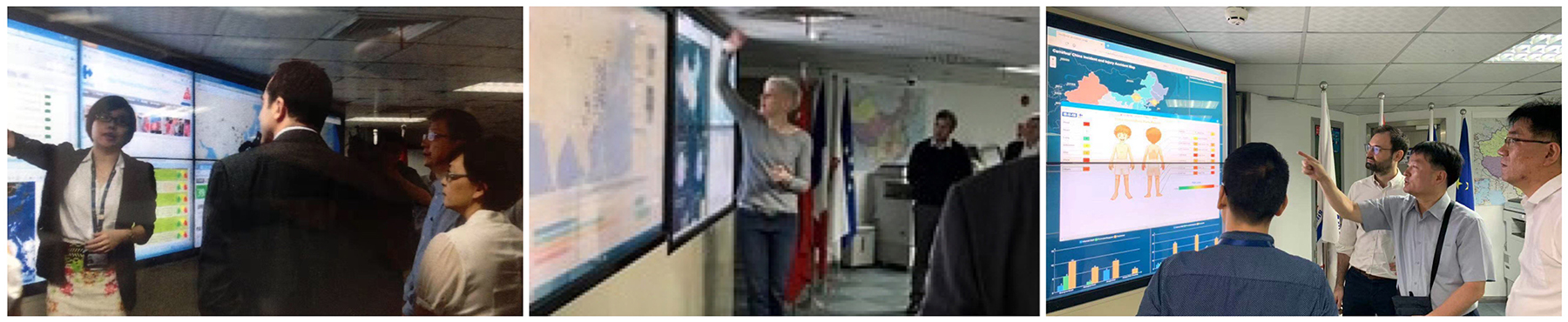
Over the years the RPMS has been shown to countless visitors: in-house managers to help them understand the importance of risk prevention, officials to show Carrefour China’s emphasis on safety, in particular food safety (see here about the visit by then-mayor of Shanghai, future Vice Premier, Han Zheng), as well as suppliers, academics, students, sometimes competitors, etc.
Show-and-tell on large touchscreens based on true data from the field proved to be a powerful tool to foster continuous improvement. A Risk Management system cannot, should not, be static and remain unchanged over the years. Instead it is a living organism that evolves with the organization and helps the organization evolve. Carrefour China, later acquired by Suning Group, constitutes a brilliant example.
Such a large scale, complex, critical project was not without challenge. It required hard work, dedication, common sense from all involved. We sincerely thank all the managers and personnel who worked with us for the RPMS project over this decade of continuous improvement and continue to work with us today!