Maintainability and reliability improvement in the automotive industry with BYJC-Fabricom
Background
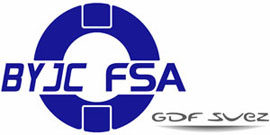
BYJC-Fabricom (www.byjc-fabricom.com.cn) is a leading supplier of turnkey automated assembly lines, primarily targeting the automotive industry. A joint-venture between Beijing Number 1 Machine Tool Plant (BYJC) and Fabricom (a specialized subsidiary of engineering giant GDF SUEZ) the company boasts an excellent track record in China with customers such as BMW, Chery Automobile, Danfoss, Delphi, Dongfeng Peugeot Citroen, FAW, Hangzhou National Panasonic, Qingdao Haier, Siemens, Valeo, Visteon, ZF, etc.
In 2008, Fabricom was contracted by German automotive supplier ZF Group to supply a new state-of-the-art production line for the manufacturing of steering columns. The same line was to be delivered to three ZF global locations (Hungary, China and the US). Initially meant to follow the first installation in Hungary, thus benefiting from the experience, the Chinese project was in fact conducted almost simultaneously, not a small challenge considering the complexity of the line and the level of multicultural cooperation required.
Faced with tight deadlines, based on the production commitments of ZF Shanghai Steering (ZFSS), BYJC-Fabricom selected Siveco China to assist in the commissioning stage of the project in order to meet the contractual reliability requirements.
A state-of-the-art production line
The Assembly Line is composed of 14 standalone stations, each station capable of producing within a cycle time of 22 seconds.
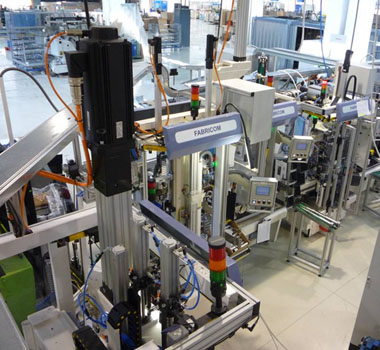
Fabricom assembly line – The most advanced and sophisticated of its category
The main stations are:
OP10/20/30: Axial rack and upper body manufacturing
OP40: Main body and crash tube assembly
OP50: Strap assembly
OP60/70/80: Transmission assembly
OP90: Radial rack fitting
OP100: Roof bracket assembly
OP120: Lever sub assembly
OP130: Lever sub assembly insertion
OP150: Test
OP160: Packing
OP40: Main body and crash tube assembly
OP50: Strap assembly
OP60/70/80: Transmission assembly
OP90: Radial rack fitting
OP100: Roof bracket assembly
OP120: Lever sub assembly
OP130: Lever sub assembly insertion
OP150: Test
OP160: Packing
The project
Siveco engineers were deployed onsite in less than two weeks and worked alongside BYJC-Fabricom and ZFSS Shanghai teams from mi-July to the end of September 2008. The Siveco team was operational after a short on-the-job training period: already familiar with Siemens Simatic technology and Kuka robots, they assisted in the commissioning and troubleshooting of the machines. Siveco was more specifically in charge of reliability improvement, maintenance preparation and the training of ZFSS operators and maintenance staff.
The following results were obtained:
– A significant reduction in commissioning time through the provision of additional resources immediately operational on the project.
– Over 300 technical failures, ranging from critical to benign, were resolved. Root cause analysis was performed on approximately 50% of them, leading to a sustainable reduction of the failure rate.
– At the end of the project, the availability of the production line reached the customer’s requirement i.e. a 90% availability rate and takt time below 23 seconds.
– The line was entirely documented in the COSWIN Maintenance System for hand-over to customer. All failures were recorded into the web-based system, ensuring complete traceability of the commissioning and early operation phase.
– Successful training of ZFSS operators and maintenance technicians.

COSWIN as a support for engineers during commissioning
According to Thierry Dormois, General Manager of BYJC-Fabricom:
“Siveco was able to quickly mobilize multi-disciplinary engineers, who successfully integrated within our multi-cultural team in a very short period of time. Under extreme pressure to start production, the involvement of Siveco ensured that we met our target in terms of line availability and maintainability.”
He added that: “Siveco China’s management remained involved throughout the project, sparing no effort to provide ZFSS and ourselves with value-added advice beyond their job scope.”