CMMS as a tool for continuous maintenance improvement for large iron pipe manufacturer in Anhui
Saint Gobain Pipelines’ Maanshan manufacturing base
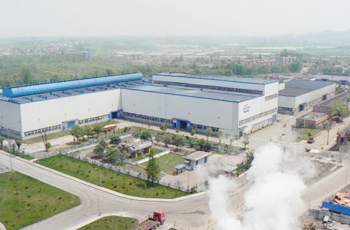
Established in 1997, Saint-Gobain Pipelines (China) owns plants located in Maanshan, Anhui Province and Xuzhou, Jiangsu Province, producing ductile iron pipes & fitting, for both the domestic and export markets. With total sales in excess of 3.5 billion RMB, Saint-Gobain Pipelines employs more than 4,800 employees in China.
With a total investment of over 100 million Euros and currently 1400 employees, Saint-Gobain Pipelines Maanshan site was established in 1997 when a JV was formed with state-owned Magang (Maashan Iron & Steel Company). Saint-Gobain later acquired the remaining shares of the company. The company produces ductile iron pipes and fittings from 100mm to 1000mm, with a total capacity of 400,000 tons.
In 2006, a blast furnace was built and started up successfully during the third quarter of 2007, allowing the company to produce its own iron marking a significant step forward for the Chinese units’ productivity and cost reduction plan. At the end of 2008, the piping plant was modernized, in order to raise its productivity. Further productivity improvements based on the group’s best practice were also launched in the foundry.
Each plant has its own maintenance department (total of over 200 staff) with, since 2008, a central site-level maintenance manager and support team. A dozen of subcontractors are also involved in the maintenance of the site.
The Siveco projects
Saint Gobain Pipelines boast a long experience with CMMS, with over 30 years’ history using such systems in its European factories. In Maanshan, the implementation of a famous CMMS software from the United States had failed a few years before: the system was never put into actual operation and quickly forgotten.
Organizing maintenance at the new iron-making plant
Siveco implemented the Coswin Maintenance Management System during the first quarter of 2007 to support the startup of the new plant, which included a blast furnace, a sintering plant, a power plant using exhaust gases and various utilities.
The aim of the project was to build a strong foundation for future operations, by supporting the creation of an accurate technical database from the project stage. Preventive maintenance plans were defined based on suppliers’ documentation and Saint-Gobain’s experience.
Coswin was also interfaced with Saint-Gobain’s ERP system Fourth Shift, later replaced by SAP, to allow for the management of parts linked to work-orders and equipments, in a totally transparent manner, so that maintenance users who see all relevant spare-parts from Coswin.
The CMMS was used from the first day of operation, ensuring ease-of-use for maintenance technicians on a daily basis through the utilization of diagrams. Based on systematic recording of failure information (what, when, impact on production), regular analysis meetings are held to optimize the maintenance strategy and to support specific decisions such as equipment replacement, design change, job frequency, change in operators TPM checklists etc.
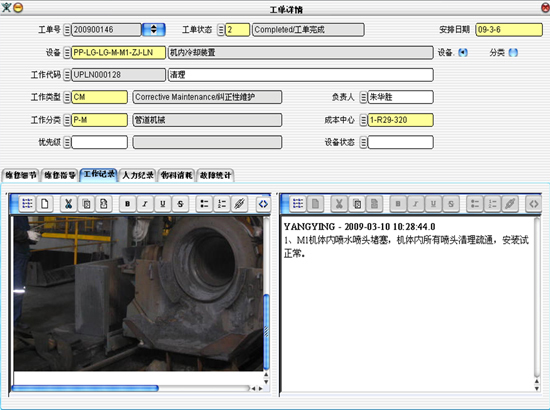
Maintenance preparation for the modernization of the piping plant
Following the success of the first project, a new contract was signed in late December 2008 to support a challenging reliability improvement project and the new organization of maintenance, with a centralized site-level manager. Following the piping plant’s ongoing modernization project, almost non-stop operation was required to meet production target in 2009, thus putting increased demand on preventive maintenance.
The Siveco project involved the rapid roll-out of Coswin CMMS before Chinese New Year, maintenance support services for the setup of optimized preventive maintenance plans in the piping plan, as well as longer-term coaching by Siveco’s maintenance experts over a one-year period. This project was also an opportunity to work more on maintenance analysis – Coswin reports based on the European standards (EN 15341, Maintenance, Maintenance Key Performance Indicators) were installed for that purpose.
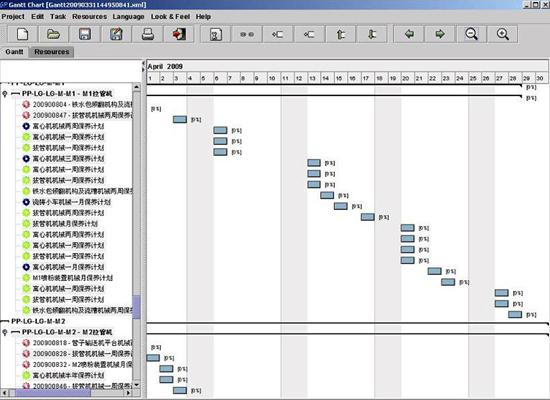
Deployment of Coswin on foundry plant
Saint-Gobain Pipelines’ maintenance team prepared all the data required to extend the system to the foundry plant, the only part of the site not yet using Coswin. The data was then migrated to the central database in just a few hours by Siveco engineers.
The foundry operates under very different constraints from the rest of the site, as it produces special fittings. It has also been selected as a pilot project for manufacturing best practices, an opportunity to further explore the analysis capability of the CMMS.
Based on the experience accumulated by the Saint-Gobain Pipeline team, this implementation required only a few days support from Siveco.
Benefits
Today the database contains over 5,000 equipments and over 644 preventive maintenance routines, for which the planning is managed in Coswin with an ongoing process to optimize maintenance tasks.
By no means a simple project, the implementation of the Coswin in Saint-Gobain Pipelines as a mean to organize and modernize the maintenance department, illustrates that year-after-year sustainable maintenance improvement can achieved in a large, complex organization in China.
Quote by Mr. Hua, Common Maintenance Manager: “Siveco’s focus on maintenance improvement rather than software has ensured continuous success to help Saint-Gobain achieve its plant management goals. Coswin is now a tool for continuous improvement at Saint-Gobain Pipelines Maanshan”