Ensuring maintenance readiness at Fushun Mining Group’s ATP project
Fushun Mining Group (“FMG”) is a large state-owned mining company located in Fushun, Liaoning Province, China. The corporation consists of about 30 companies focused on coal mining and oil shale processing, with a total of around 28,000 employees. FMG is one of the world’s largest oil shale producers: it owns 3.5 billion tons of geological reserve for high grade oil shale, of which the exploitable reserve is 560 million tons. The company operates the largest oil shale plant in the world consisting of 220 sets of Fushun-type retorts, with annual shale oil yields of 330,000 tons. In this process, finer particles of oil shale are discarded, resulting in waste and environmental pollution.
To make full use of its resources, FMG invested 800 million RMB to build the first Alberta Taciuk Processor (ATP), designed by a Canadian subsidiary of ThyssenKrupp Technologies, to treat small-size oil shale that can’t be processed in Fushun retort, with a capacity of 6,000 tons per day.
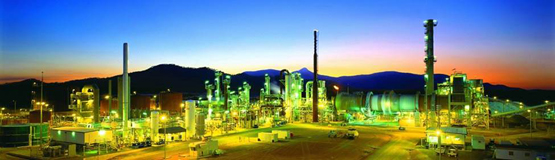
From construction to maintenance, specific challenges
ATP construction started in early 2006 and was completed in 2010. Commissioning took several years to complete until late 2012, reflecting the great complexity of the facility. FMG’s management team, recognizing the maintenance challenge presented by the new plant and its imported technology, decided to tackle the problem and contacted Siveco. China’s largest maintenance consultancy, Siveco is known to have pioneered the concept of implementing maintenance systems during the construction of a plant, thus supporting start-up and enforcing good maintenance practices from day one.
Typical plant documentation and maintenance preparation challenges, met in construction projects all over the world, tend to be exacerbated in China, where operators lack the long track record of their Western counterparts. In addition, greenfield projects in China often present specific challenges, as for the ATP plant its uniqueness, size and complexity.
FMG also realized that simply cutting and pasting a Western management model would not work in China. Foreign engineering companies involved in Chinese projects, especially those lacking local experience, often fail to recognize the specific needs, strengths and weaknesses of Chinese maintenance team, and get bogged down in misunderstandings. Siveco, with its in-depth knowledge of “maintenance with Chinese characteristics” was a good match for this project.
Building the maintenance system
FMG hired Siveco to implement the new plant’s maintenance management system in time for startup. The contract was signed in June 2012 covering the maintenance system itself, as well as start-up assistance to ensure smooth handover from commissioning to operation.
Specific goals for the project included:
– Building a complete plant database, to avoid omissions or mistakes in the transfer of technical documentation from construction to maintenance.
– Ensuring work safety, through strict operating procedures and tracking of employees’ qualifications and licenses.
– Enabling feedback from event and failures (symptoms, failure, actions, etc.), in order to create usable historical records for improvement purposes.
– Implementing the preventive maintenance strategy from the first day of the operation and developing good habits of regular analysis.
– Ensuring work safety, through strict operating procedures and tracking of employees’ qualifications and licenses.
– Enabling feedback from event and failures (symptoms, failure, actions, etc.), in order to create usable historical records for improvement purposes.
– Implementing the preventive maintenance strategy from the first day of the operation and developing good habits of regular analysis.
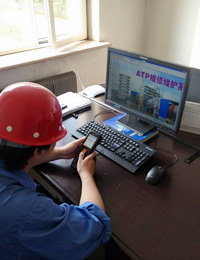
ATP implemented Siveco’s mobile solution bluebee® “for the worker of tomorrow” to support daily maintenance work.
To achieve these objectives, Siveco implemented a maintenance management system (CMMS), integrated with a document management system (DMS) and a mobile solution for plant inspections. The Siveco project team provided maintenance engineering services onsite, working alongside the ATP maintenance team for a five months period, until the system was put into use in December 2012.
The maintenance system, ready for startup
By the end of the project, FMG’s objectives were achieved:
– The plant was fully documented in the CMMS and DMS, including equipment structures and related documentation, technical specifications, spare-parts lists, contracts, standard work instructions, etc. The entire database was built on standard coding rules, allowing quick retrieval of information.
– The system provides full support and traceability of work procedures: maintenance work orders, work permits, inspections. The bluebee® mobile solution, used for plant inspections, enables strict supervision of field work through scanning of barcodes and onsite data capture, without having to rely on paperwork.
– The work order system ensures incidents and work done are reported in a structured manner, to form comprehensive and usable historical records. The planned maintenance system allows automatic generation of preventive maintenance schedules and an assessment of their execution.
– Finally, Key Performance Indicators (KPIs) and analysis reports were defined in the system, to support the maintenance team’s regular review meetings. Reports comply with the international standard EN 15341 Maintenance Key Performance Indicators.
– The system provides full support and traceability of work procedures: maintenance work orders, work permits, inspections. The bluebee® mobile solution, used for plant inspections, enables strict supervision of field work through scanning of barcodes and onsite data capture, without having to rely on paperwork.
– The work order system ensures incidents and work done are reported in a structured manner, to form comprehensive and usable historical records. The planned maintenance system allows automatic generation of preventive maintenance schedules and an assessment of their execution.
– Finally, Key Performance Indicators (KPIs) and analysis reports were defined in the system, to support the maintenance team’s regular review meetings. Reports comply with the international standard EN 15341 Maintenance Key Performance Indicators.
According to Director Sun Yongshu: “Our maintenance system covers both the front-end (technicians working onsite) and the back-end (technical management team). Already considered a milestone in the industry, this project provides critical support for the long-term operation of this technologically-complex plant by our local team.”
Siveco China has an extensive track record helping companies prepare maintenance before startup. Already published customer stories include:
Alstom Wuhan Boiler Company
BYJC-Fabricom for ZF Shanghai Steering
Daramic Xiangfan Battery Separator
New French Embassy in Beijing
Ranhill Powertron II (RPII) Power Plant
Saint Gobain Pipelines Maanshan
Shanghai Sogefi Auto Parts
SCIP Swire SITA Waste Services
Alstom Wuhan Boiler Company
BYJC-Fabricom for ZF Shanghai Steering
Daramic Xiangfan Battery Separator
New French Embassy in Beijing
Ranhill Powertron II (RPII) Power Plant
Saint Gobain Pipelines Maanshan
Shanghai Sogefi Auto Parts
SCIP Swire SITA Waste Services