Leading PVC maker revolutionizes its inspection process, adds value to SAP
Hanwha Chemical (Ningbo)

Hanwha Chemical (Ningbo) was established in 2008 in the Ningbo Daxie Development Zone, a national-level economic and technical development zone in Zhejiang province, as a subsidiary of Fortune 500 Company Hanwha Group (www.hanwha.co.kr), a diversified Korean conglomerate. Hanwha Chemical was the first producer of polyvinyl chloride (PVC) in Korea in the 1960s, a pioneer that laid the groundwork for the nation to emerge as a leading chemical producer: the history of Hanwha Chemical epitomized the history of the petrochemical industry in Korea.
With a total investment of 363 million USD, the Ningbo plant is the largest foreign-invested project in the zone and one of Hanwha Group’s largest investments outside of Korea, targeting the world’s largest PVC market, China. Production started in December 2010. The plant boasts an annual production of 0.3 million tons of PVC, 0.5 million tons of EDC, and 0.3 million tons of VCM, with an annual sales revenue of approximately $ 2.3 billion.
The challenges of optimizing the inspection process
Hanwha Chemical’s complex chemical production units operate around the clock and face tough safety, environmental and mechanical integrity regulations: ensuring reliability, availability and safety is at the core of the company’s business. The Ningbo plant has established good operation and maintenance practices, based on the group’s long experience and the know-how accumulated by its local engineers and technicians. Preventive maintenance, more particularly in the form of inspections to detect early signs of failure and monitor process parameters, plays the major role in the company’s operation. Hanwha has also implemented SAP, the de-facto ERP standard in the petrochemical industry, including SAP Plant Maintenance module to support its maintenance process.
As often observed in the chemical industry, however, the management of inspections, both operation and maintenance checks, measurement rounds, tends to fall in the gaps of the IT system and is left to rely on technicians’ individual know-how and sense of duty.
Equipment structures in SAP, the implementation of which is usually financial-driven, are often not detailed to the necessary level (individual components like valves, inspections and measurements points) and the associated instructions and documentations are usually managed in other databases or on paper. The “Work Order”, designed to capture costs related to maintenance tasks, is not suited for simpler daily routine checks. Finally, the usage of SAP PM is, in most cases, limited to maintenance supervisors and “system secretaries” assigned to input data from paper reports. It does not reach the operation and inspection teams, less accustomed to using complex IT systems in their daily work. Most chemical plants face the same challenge when it comes to managing inspections, assessing their executions and handling feedback in a useful manner:
• Difficult to control and track work execution (has the inspection really be done?)
• Less accurate reporting or measurements (often handwritten report on paper)
• Results and measurements are not usable for analysis (paper reports get archived in folders, analysis would require manual input into a system, sometimes done in Excel or in separate, specialized subsystems)
• Less accurate reporting or measurements (often handwritten report on paper)
• Results and measurements are not usable for analysis (paper reports get archived in folders, analysis would require manual input into a system, sometimes done in Excel or in separate, specialized subsystems)
As a result, the inspection loop is hard to close: significant gaps exist between the definition of inspection routines, the planning process, the execution and reporting process and finally the analysis and optimization process. Support from traditional IT systems, designed for administration and cost control, is severely lacking.
The Hanwha Ningbo team quickly came to the realization that new innovative tools were needed to support the daily inspection process, so critical for the plant operations.
Solving the problem
Faced with these challenges, Hanwha’s VCM (Vinyl Chloride Monomer) operation team launched a project to search for the ideal tool to support their inspection and measurement rounds: they envisioned field technicians using mobile devices to carry out their daily work.
The project team conducted an extensive review of hardware and software vendors, to find that most of them were IT developers or hardware makers without knowledge of their industrial requirements, proposing to custom-develop whatever Hanwha would specify, a solution described as “using PDAs to access a database”. This approach carried all the risks associated with IT development projects and did not meet Hanwha’s expectations: finding the right supplier had become another challenge. This is when Hanwha engineers came across an article in a technical magazine, featuring a case study of Sichuan Lutianhua, a large fertilizer plants using Siveco’s mobile solution, known as bluebee®, to optimize inspections. A few months later, in September 2011, Hanwha signed a contract with Siveco, a company uniquely positioned in using high-tech to solve real-life maintenance problems, for the implementation of bluebee®.
The goals of the project were direct answers to the challenges faced by Hanwha:
• To ensure that jobs are actually performed, through mandatory scanning of asset tags
• To provide a diagnosis aid for technicians, based on reported symptoms and access to existing know-how
• To allow analysis of measurement trends, in order to predict failures
• To use operation and management reports to optimize inspection plans, ultimately enabling a Risk Based Inspection (RBI) strategy
• To provide a diagnosis aid for technicians, based on reported symptoms and access to existing know-how
• To allow analysis of measurement trends, in order to predict failures
• To use operation and management reports to optimize inspection plans, ultimately enabling a Risk Based Inspection (RBI) strategy
The project was launched in middle of October 2011 and successfully went live at the end of the year.
The bluebee® project
Siveco provided a complete turnkey solution including maintenance engineering services, the bluebee® software, hardware (mobile devices, PC server and barcode printer) as well as equipment tags (stainless steel plates).
PDA devices from Korean supplier Bluebird were selected, optimized to run bluebee® and equipped with 2D imagers for asset identification.
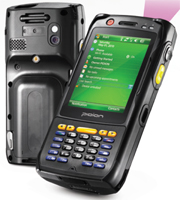
Two Siveco project managers were appointed, one focused on overall project management and maintenance improvement, the other on the delivery of the system. The Siveco back-office team, located in Shanghai, dedicated three people full-time to support the project.
Thanks to bluebee®, inspection technicians receive their inspection tasks and related specific guidelines on their PDA and, after scanning the tag of the corresponding asset or inspection point, record results directly in the device. For example, operation staff can input operating parameters observed during their daily walking inspection routine on pumps (outlet pressure, temperature, oil level, unusual sounds, visual checks of seals etc.). bluebee® will provide immediate feedback on abnormal readings and further assistance can be obtained if needed. All data will be summarized and analyzed in the back-office management system, also producing regular reports for management (monitoring execution) and analysis (improvement of plans and strategy) purposes. The process is shown below:
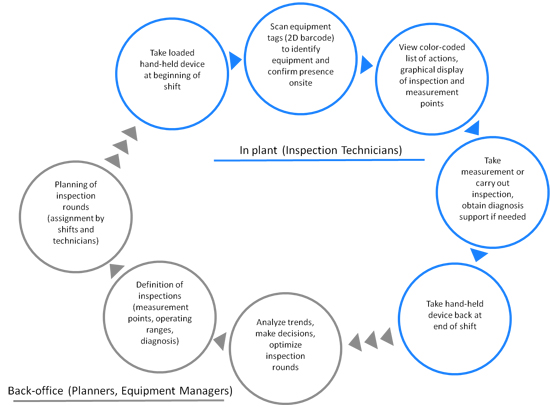
During the implementation, Siveco organized an exchange visit between the Hanwha VCM team and Sichuan Lutianhua. Such visits, opened to all Siveco customers, are meant to promote experience sharing between different plants and have proven very successful. For more information about Lutianhua, see the case study.
What are the main differences between the Hanwha and Lutianhua projects?
• Main focus: Lutianhua uses bluebee® for maintenance inspections, while Hanwha uses bluebee® for daily operation inspections.
• Inspection planning: in Lutianhua, tasks carry various frequencies of execution and thus require using the back-office planning module to schedule and assign tasks automatically, while in inspections by the operation team have a 4-hour frequency, which do not require scheduling – the focus is purely on execution and reporting.
• Telecommunication requirements: Lutianhua is using the public 3G mobile network for bluebee® devices to connect to the back-office system in real-time, while Hanwha chose to synchronize data when PDA are put back into their cradle when the operator is back at the office – indeed, the plant’s potentially explosive atmosphere prohibits the use of wireless communication (ATEX directives).
• Reporting process: in Hanwha, whenever abnormal circumstances appear, the inspector can take a photo with the PDA camera to create a work request in the back-office system; the manager can then immediately view it and launch related activities through his daily work wizard screen. In Lutianhua, focus is not on triggering corrective actions. Instead, when something needs to be fixed, a Work Order is entered manually in their CMMS Maximo.
• Inspection planning: in Lutianhua, tasks carry various frequencies of execution and thus require using the back-office planning module to schedule and assign tasks automatically, while in inspections by the operation team have a 4-hour frequency, which do not require scheduling – the focus is purely on execution and reporting.
• Telecommunication requirements: Lutianhua is using the public 3G mobile network for bluebee® devices to connect to the back-office system in real-time, while Hanwha chose to synchronize data when PDA are put back into their cradle when the operator is back at the office – indeed, the plant’s potentially explosive atmosphere prohibits the use of wireless communication (ATEX directives).
• Reporting process: in Hanwha, whenever abnormal circumstances appear, the inspector can take a photo with the PDA camera to create a work request in the back-office system; the manager can then immediately view it and launch related activities through his daily work wizard screen. In Lutianhua, focus is not on triggering corrective actions. Instead, when something needs to be fixed, a Work Order is entered manually in their CMMS Maximo.
The results: three layers of benefits
First layer – enabling critical maintenance engineering activities
Hanwha experienced the first benefits of the bluebee® project during the implementation itself, as the inspection team was immediately fired up by the use of high-technology. As a direct consequence, awareness of best practices increased. The project prompted a more in-depth definition of equipment structures and inspection points, at a level of detail which did not exist in SAP PM; bar-coded steel tags were physically attached on the equipment, ensuring exact match between the database and the reality. A continuous improvement process was initiated based on a systematic analysis of data collected in the field, something which was practically impossible to achieve using a traditional paper-based process.
Second layer – immediate improvement in accuracy and traceability
Once bluebee® was put into day-to-day service, it provided a range of immediate operational benefits both from the technical and management point of view. Inspectors saw the accuracy of their records improved, as bluebee® clearly indicates inspection points, requires scanning of barcode for confirmation, warns users in case of abnormal readings and provides basic diagnosis support. Any unfinished action is clearly visible in the mobile display, through simple color warnings. From the management point-of-view, bluebee®‘s back-office system keeps track of job completion and back-logs. Management and analysis reports can be sent automatically by email or queried from any PC. Thanks to physical barcode scanning, the technicians’ presence at the inspection point is assured, greatly enhancing compliance with regulations and safety standards, critical in the chemical industry.
Third layer – optimization and beyond
Longer term ROI in terms of reliability and availability will derive from regular analysis of data and the resulting optimization of the maintenance strategy. The project has achieved the necessary steps to implement a true Risk Based Inspections (RBI) strategy based on real data from the field, which is seldom seen in the industry.
According to JANG Sang Moo, Senior Manager of VCM production team:
“bluebee® has already helped our team achieve excellent results. The project has not only received great feedback from users, but also praises from our top-level management in Korea. Based on our successful experience in VCM, the PVC division has decided to start its own bluebee® project in 2012.”
Read “Siveco partner” article to know more about Bluebird’s handheld devices.