Obtaining ROI from maintenance optimization at mobile phone giant in Beijing
This case study, written before the acquisition of Nokia by Microsoft, represents a great example of optimizing maintenance costs in tough economic times.
Siveco’s first encounter with Nokia was during the company’s heydays, when the LEED Gold certified Nokia Beijing campus was the center of attention in the Facilities Management community. The facility featured gym, nurseries, community centers and a variety of social spaces. Many different FM service suppliers were working on the project, including strategic asset management consultants from the US, all enjoying the seemingly unlimited wealth of the successful telecom giant.
Unfortunately, times got tougher… As sales volume went down, Nokia became concerned with cost control and maintenance was rightly identified as a priority. It is in this context of slowing, uncertain business, that Nokia contacted Siveco, with the initial aim of reducing spare parts cost… After an onsite assessment, Siveco proposed a phased approach to optimize maintenance costs. This Customer Story tells about the project Siveco conducted with Nokia and the significant cost savings obtained.
Nokia’s business sadly did not recover the crisis and the company was sold to Microsoft. During the entire project period, the Siveco team never met any of the famous consultants and FM suppliers previously involved during the company’s golden days. Siveco never came across any document or procedure written by those strategic consultants and experts. When times got tough, they were all gone… As the overall Chinese economy shows signs of slowdown, the experience of Siveco at Nokia Beijing demonstrates that maintenance represents a great opportunity for savings through optimization.
Nokia Beijing
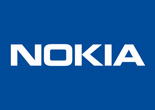
Nokia (www.nokia.com) is a global leader in mobile communications whose products have become an integral part of the lives of people around the world. Nokia’s technological and design innovations have made its brand one of the most recognized in the world. Nokia operates a modern production facility located in Beijing Economic & Technological Development Area (BDA), part of the well-known Nokia China Campus built in 2008.
Nokia’s Customer Fulfillment Operations (CFO) is responsible for final assembly and testing. A large organization with several thousand employees, hundreds of which work in maintenance, CFO employs most of the plant’s personnel. While turnover is moderate (up to 10% for technicians) thanks to Nokia’s favorable policies, the company faces the typical challenges of the Chinese maintenance market, including a lack of multidisciplinary skills, making workload balancing difficult.
Production is characterized by the relatively short commercial life of products (1 year), frequent product changes, a highly variable production volume (fluctuating demand) and a very lean production process, based on just-in-time principles. In such an environment, “No production means no maintenance; no maintenance means no production”.
The initial project – taking it upside down
In 2010, Nokia Beijing launched a supplier selection to install a computerized inventory system for the management of repairable equipments, tools, spares and consumables. Various IT vendors were considered, among them software development companies, CMMS/EAM suppliers and ERP vendors. Towards the end of 2010, Siveco was consulted and proposed to turn the project upside down: what was the actual pain?
Nokia decided to hire Siveco to conduct a maintenance assessment to identify the real ROI opportunities and to make relevant commendations for the implementation of supporting systems. Based on the conclusion of the 2-week onsite assessment by Siveco experts, the joint Siveco and Nokia team defined a multiphase project aimed at achieving the best possible ROI.
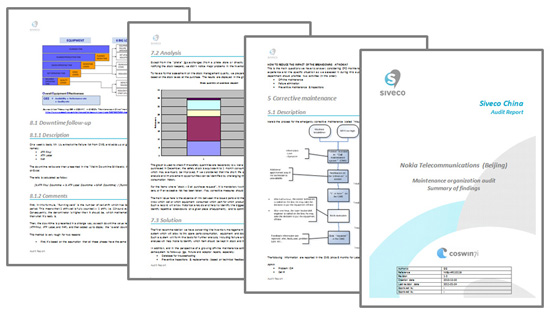
Nokia Audit Report
The implementation – maintenance expertise, IT tools
The first phase of the project was to focus on building a standard maintenance platform around an equipment database using Siveco’s “COSWIN” CMMS. The utilization of the system covered second-line maintenance, including standard exchanges, workshop repairs, spare parts and purchases. Work processes were redefined, with KPIs and reports aimed at assisting the Nokia team to meet their improvement objectives.
For this part of the project, Siveco was onsite for 3-month period, followed by regular onsite coaching sessions. The Siveco team consisted in a project manager (maintenance manager with multidisciplinary background), providing consulting and strong guidance for the project, with a focus on ROI; a maintenance engineer (automation background), for the day-to-day coaching, acting as a user; a CMMS engineer (multidisciplinary background), for system configuration as needed and training. The Nokia project team comprised the department manager as project manager, with a strong business focus, result-oriented; and project team members: key engineers from various departments. Other departments were involved, helping them to gain an understanding of the project (finance, purchase, top management).
At the 1-month follow-up review, ROI was considered obtained from phase 1. The team obtained agreement from top management to continue the project, with better data to estimate ROI from future phases. Multiple small phases, or implementation packages, were defined in order to reduce risk, in relation to Nokia’s highly variable business environment. A target ROI was estimated, and committed to by the joint team, for each implementation package, with the idea to prove ROI before moving on to the next package.
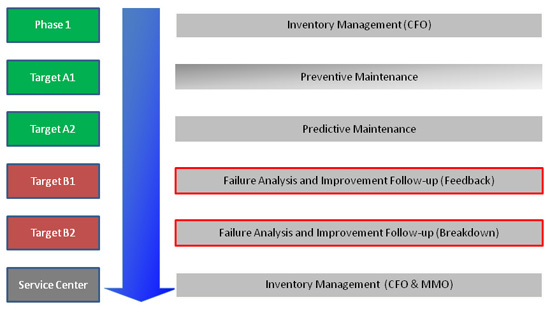
All the phases in Nokia project
The project is currently (June 2012) in an advanced stage dealing with preventive and predictive maintenance, failure elimination and first line maintenance.
Results obtained
As Nokia’s maintenance cost was well within benchmarks, the main focus was not put on cost reduction but rather on the impact of maintenance activities on production volumes.
According to Nokia’s own estimates, the following results were obtained from the first phases of the project:
– Downtime rate reduction by 15% (target was 7%)
– MTBF increase by 12.7% (target was 5%)
– Inventory accuracy increased from 67% to 96% (stock value remained stable)
– MTBF increase by 12.7% (target was 5%)
– Inventory accuracy increased from 67% to 96% (stock value remained stable)
As a company like Nokia is naturally very secretive with their financial information, we cannot reveal the cost of downtime that would allow us to calculate savings (however our readers could make their own estimates). A very rough calculation only taking into accounts the time saved by production operators and approximate operators salary adds up to 500k RMB per year – this is really the tip of the iceberg. For more on ROI estimates, see the Reliability article: Show me the money! How to financially justify maintenance projects to top management.
According to Li Zhihong, Maintenance Manager, “Siveco’s performance-driven approach was very well-matched with our own company culture and Siveco gained our trust by hard work and results. Thanks to the CMMS we now have access to reliable data, giving us a much clearer view of the performance of CFO maintenance teams. While management is satisfied with results, the project has also gained positive attention from other plants in Nokia’s supply chain. Last but not least, the end-users, our engineers and technicians, are happy with the project and benefit from improvement in their daily work and opportunities to enhance their maintenance skills.”