Practical maintenance improvement supports production ramp-up at leading heat exchangers manufacturer
Fives Cryo (Suzhou)
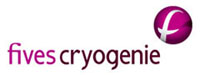
Fives Cryo manufactures brazed aluminum plate-fin heat exchangers used in industrial gas processes for air separation units, hydrocarbons separation, ethylene production, natural gas liquefaction by cryogenic process and low-temperature refrigeration. The Suzhou plant started operations in September 2009, following its historical customer Air Liquide.
The initial focus of Fives Cryo Suzhou was on starting production and ensuring the first deliveries. Once fully up-and-running, the company started signing new customers and ramping up production volume, thus putting more pressure on maintenance. As many manufacturers in the East China region, the company is faced with high staff turnover, which proves a major challenge in its development. From an equipment perspective, two critical machines (degreasing unit and furnace) constitute bottlenecks, with major impact on production in case of breakdown (no available backup on-site). The maintenance department consists of 6 people in charge of repairs and preventive maintenance including lubrication, inspections, etc., while more specialized work is usually outsourced.
The maintenance improvement project
The main pains experienced by Fives Cryo were constant operation in “firefighting” mode due to lack of planning. At the same time, the data needed to make decisions such as technical improvement, machine modifications, maintenance budget, recruitment needs and so on was lacking.
Fives Cryo (Suzhou) started working with Siveco on March 2012, with a maintenance project designed to build up a structured and sustainable maintenance organization. The ultimate goal of the project was to improve the availability of the machines, as the production output rose, and to extend their lifetime.
A computerized maintenance management system (CMMS) was implemented to structure the maintenance team around clear work processes, reporting requirements and regular meetings (daily work, weekly planning, monthly analysis etc.). By providing measured indicators of performance, it allows the team to start working on improvement maintenance. This principle is shown in the figure below:
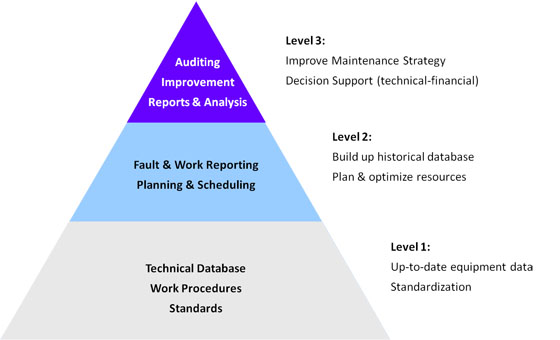
The Siveco Approach
This system-based approach, pioneered by Siveco China in the mid-2000s, has proven particularly successful in China where maintenance engineers lack methodological background – the implementation of a “real” system helps them grasp the various concepts associated with maintenance (a systematic approach, preventive maintenance, analysis and decision making). Typical customers experience Return On Investment (ROI) within the first year.
Scheduling and first results
The project was executed in a 3-month implementation period, followed by audits after 1 and 2 months, after which the plant entered an “Enhanced Support Period” (for more on Siveco Enhanced Support, please see here) during which Siveco experts remotely monitor performance thanks to the CMMS, provide necessary guidance and come back for a yearly onsite audit. The project involved the top management, as well as the Production,
At the beginning of the support period, Fives Cryo had already achieved significant benefits. The immediate project goals were met, namely:
Establishment of the plant’s asset database
More than 800 pieces of equipment, technical specifications, related spare parts, documents and contracts, were documented in the CMMS, based on the principles of the ISO 14224 and ISO/IEC 81346 standards. The impact is visible outside of the system as equipment codes defined are now used on paper documentation as well. Spare parts codes have been unified between SAP and the CMMS, allowing efficient collaboration between maintenance, procurement and accounting departments. Standardized job guidelines were created for preventive maintenance tasks.
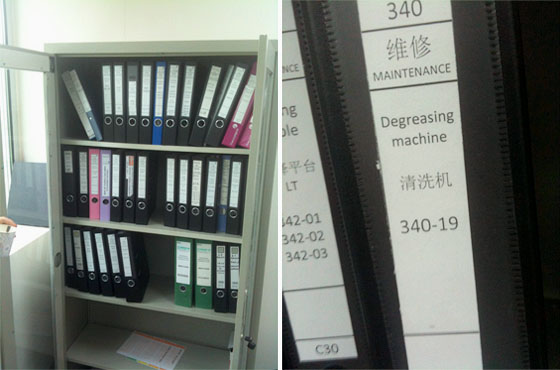
An example of the structuring impact of the CMMS on the maintenance organization:
Equipment codes defined during implementation are now used on the documentation folders.
Training of the maintenance team on key concepts
The team was trained both through classroom training and hands-on through the project and using the CMMS. Training covered plant documentation, fault reporting, work orders, preventive maintenance, regular meetings and improvement process. The staff ability to manage preventive maintenance in a structured way, though plans and work orders, was assessed.
Ensuring that all failures are reported and coaching the team on creating a preventive maintenance plan and follow it up in the system
At the time of the second audit, 70% of the work orders in the system had comprehensive feedback – an excellent result by any realistic standard – and quality was shown to be improving. As a result, the team is now able to perform root cause analysis and to make technical-financial decisions based on the maintenance history in the system. In addition an average of 80 hours/month of preventive maintenance activity were reported, consistent with reality – to be compared to the situation before the project when preventive maintenance was not formally defined and virtually inexistent.
Using reports generated from the system to support regular meetings and improvement process
By the time of the second audit, the first improvement analysis session was performed using the system, by Fives Cryo’s maintenance team, with the assistance of Siveco experts. Regular team meetings were now in place, conducted by Fives Cryo’s own team.
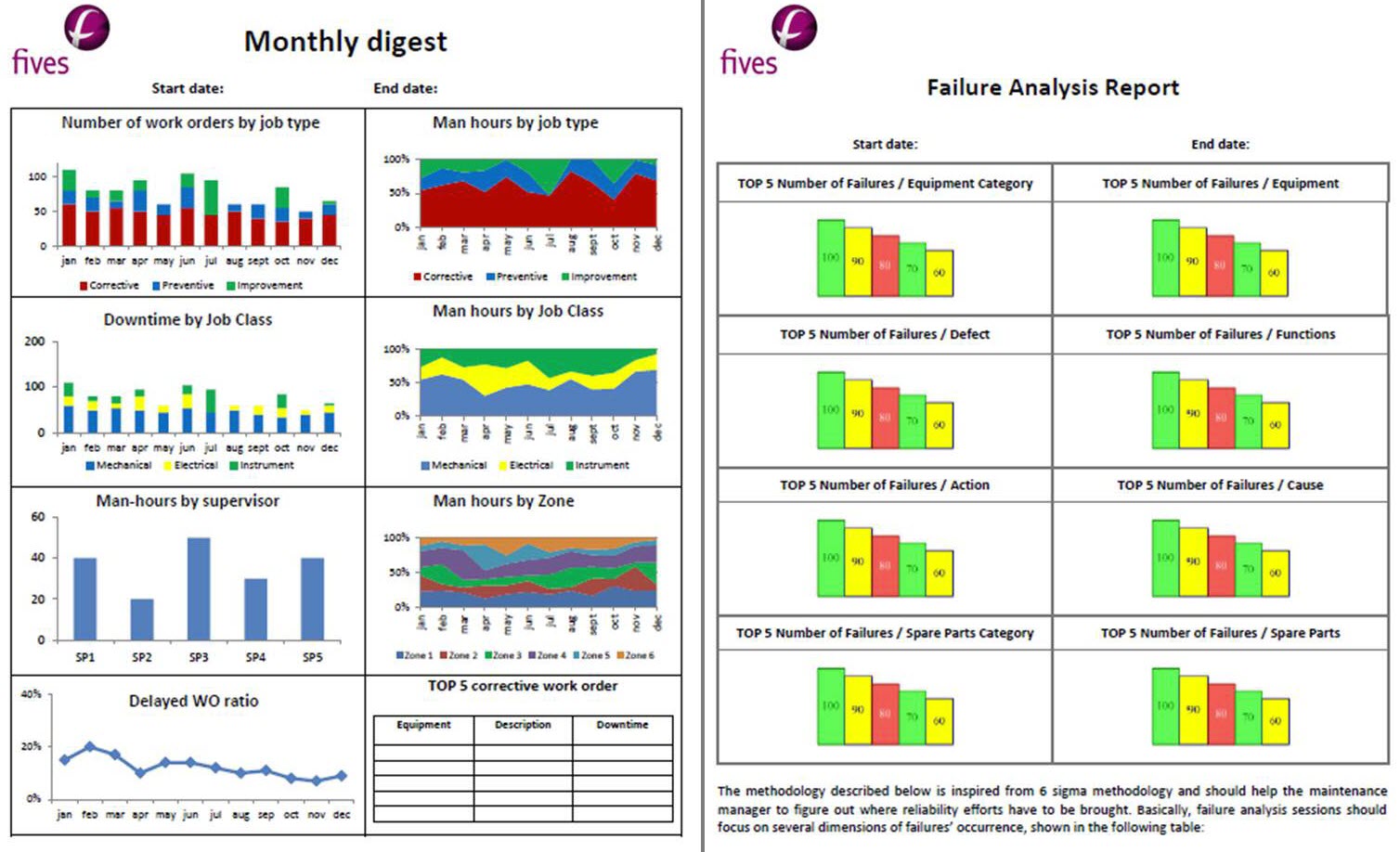
Sample management reports obtained at Fives Cryo
The road ahead
As the project has entered its final phase, with an ongoing “enhanced maintenance period” – during which Siveco experts provide remote audit and support, while coming to site at least once a year – the Fives Cryo team has grown confident about using the CMMS to manage its maintenance.
According to Jean-Yves Lacroix, Engineering Director at Fives Cryo:
“The work already done with the Siveco team has really put our maintenance team on the right track towards preventive maintenance and the monthly report helps drive this new attitude. From a management perspective, we clearly see how the system will be used in the longer term (a year or so) to assess the need to outsource some of our maintenance, with hard technical and financial data in hand, or to recruit internally if necessary. The accurate historical database will also help us negotiate contracts with spare-parts suppliers.”

Benefits summary after 2 months – 80 hours/month of preventive maintenance were reported – to be compared to the situation before the project when preventive maintenance was not formally defined and virtually inexistent. – The team is now able to perform root cause analysis and to make technical-financial decisions based on the maintenance history in the system. – Standardized job guidelines were created for preventive maintenance tasks. – Spare parts codes have been unified between SAP and the CMMS, allowing efficient collaboration between maintenance, procurement and accounting departments. Benefits summary after 6 months – Average of 174 work orders are recorded every month, based on which technical data analysis is conducted in a structured manner once a month. – The share of Preventive Maintenance (in percentage of time spent) increased from less than 10% initially to around 60%. |
The results after 6 months demonstrate how the strong foundation established during the project is leading to actual improvement results (increased share of Preventive Maintenance). For confidentiality reasons, no financial figures are provided in this customer story, astute readers can however compute their own savings estimate…
The simplest calculations are often the best. As a rule-of-thumb, well accepted in the industry, planned work (preventive) is at least 50% more efficient than unplanned work (corrective), i.e. approximately 50% less costly. Assuming a hypothetical annual maintenance cost of 1 million, a calculation shows the increase in preventive maintenance results in 300k savings. For more on ROI calculation, see this Reliability article: Show me the money! How to financially justify maintenance projects to top management.