Start-up maintenance support for new Sino-US manufacturing plant
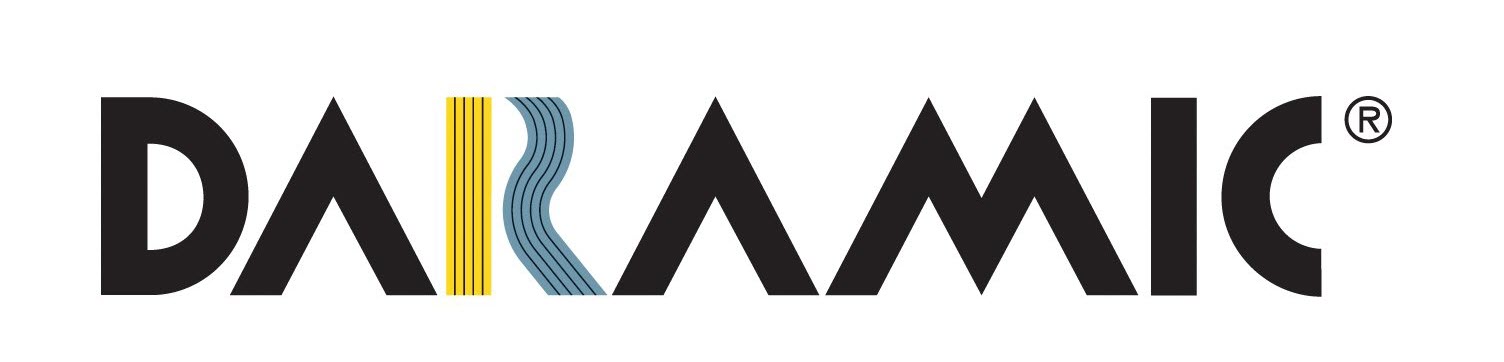
Daramic Xiangfan Battery Separator Co., Ltd.
Daramic (www.daramic.com) is the world’s leading manufacturer and supplier of battery separators for automotive, industrial, and specialty applications. Established over seventy-five years ago, the company services the global battery manufacturing industry through marketing and sales offices in North and South America, Europe, Australia, South East Asia and China. As a business unit of Polypore, Inc.—with headquarters in Charlotte, North Carolina USA—Daramic today supplies more than 50% of the world’s demand for high performance polyethylene battery separators to the lead acid battery industry.
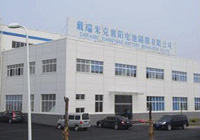
In order to consolidate its leading position in China, Daramic signed in 2010 a joint-venture Agreement with the largest local Lead Acid Battery manufacturer. The joint-venture company – Daramic Xiangfan Battery Separator Co., Ltd. located in Xiangyang, Hubei province.
To better serve the local market, the joint-venture company has built a new facility with two production lines, representing 35M sqm of capacity, in a two-step process. Most equipment was imported from Europe.
Siveco’s one-year mission
Daramic selected Siveco to provide maintenance engineering services for the new plant. A long term contract was established to dedicate a Siveco consultant for a one-year full-time mission, to support the implementation of good maintenance practices during the plant start-up, offering a various range of services, including but not limited to:
• Definition of the maintenance strategy
• Organization of the maintenance department
• Building up of the spare-parts stock
• Development of troubleshooting and preventive maintenance guidelines
• Implementation of maintenance methodologies
• Setting up accurate technical documentation
• Start-up assistance for the production line
• Organization of the maintenance department
• Building up of the spare-parts stock
• Development of troubleshooting and preventive maintenance guidelines
• Implementation of maintenance methodologies
• Setting up accurate technical documentation
• Start-up assistance for the production line
The appointed Siveco consultant was immediately deployed onsite in Xiangyang, at the beginning of June 2012.
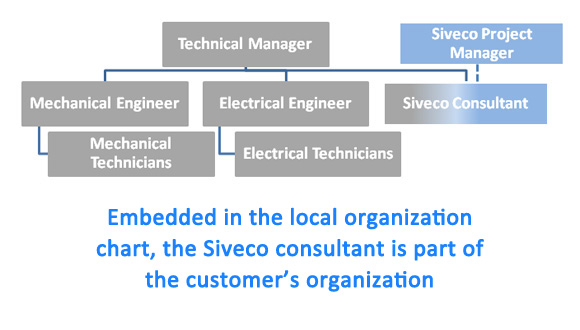
Building an efficient maintenance organization
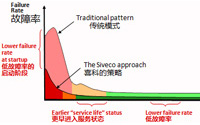
The first months of production are always challenging in a new factory: the technical team struggles with the many early-life failures on newly installed equipment. Working days are full, nights are shorts… In spite of the heavy technical workload, the administrative aspects of preparation should not be forgotten. Being well organized from the start is the key to get rid of the dreaded “fire fighting mode”.
One of the roles of the Siveco consultant is to take a step back from the day-to-day events and to advise the local technical manager on how to organize an efficient maintenance department. As the factory is new, all the procedures had to be written; all the management tools and others KPIs needed to manage production had to be set up.
Thanks to his experience and that of the entire Siveco back-office, the embedded consultant brings with him many ready-made templates such as:
• Work permit
• Technical improvement request
• Work safety management (LOTO)
• Technical improvement request
• Work safety management (LOTO)
The templates are then adapted to the specificities of the local organization, a necessary step to ensure their smooth utilization.
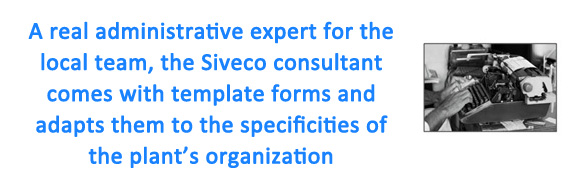
Localizing spare parts procurement, a risk-based approach
Having the right spare parts in stock at the right time is the first requirement to ensure reliable operation of the production line. In Daramic’s case, with second-hand equipment coming from Europe, spare parts proved to be a major challenge. How to replace references that are no longer produced by the suppliers? How to handle the very long and irregular lead-time to deliver imported parts into China? How to maximize the use of Chinese-made parts to replace costly European parts?
The Siveco consultant was put directly in charge of leading a review of safety stocks and implementing related actions:
• A criticality analysis was performed for each PID (Process and Instrumentation Diagram) of the plant, to establish the list of critical parts in a systematic manner.
• A weekly KPI was defined to follow up progress.
• The final Critical Spare Parts list contained more than 250 references of critical spare parts.
• For each critical spare, a risk assessment was done as to the possibility to localize its procurement, weighing in critically, cost, lead time, quality, and after-sales service issues.
• A weekly KPI was defined to follow up progress.
• The final Critical Spare Parts list contained more than 250 references of critical spare parts.
• For each critical spare, a risk assessment was done as to the possibility to localize its procurement, weighing in critically, cost, lead time, quality, and after-sales service issues.
The Siveco consultant, thanks to his long maintenance experience both in China and Europe, is uniquely positioned to assess the advantages to keep a European supplier or to switch to a local one, based on the systematic risk analysis.
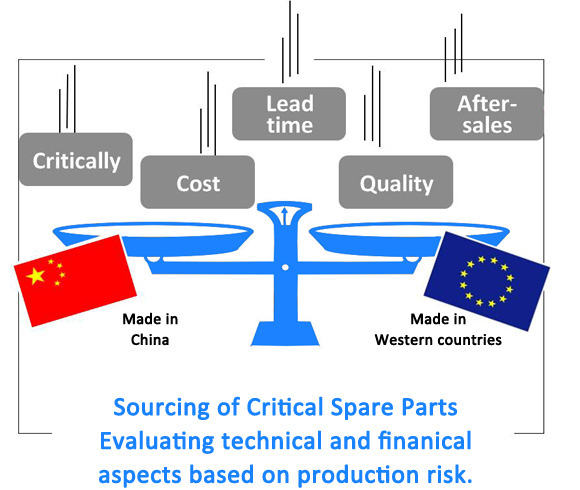
Continuous improvement
As soon as production started, the Siveco consultant set the continuous improvement process in motion. Inspired by TPM methods, a downtime record file was implemented: every week a meeting is held to analyze every single event and to define corrective and preventive actions. The Production and Technical departments, but also EHS when needed, work hand-in-hand during the downtime analysis sessions, to achieve results that will benefit everyone in the plant.
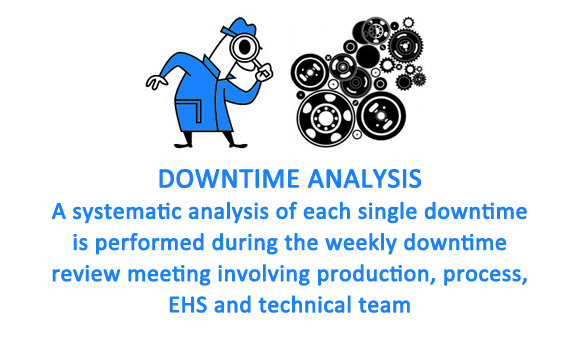
A consultant in working overall
According to Zhanjun Zhao, the General Manager of Daramic Xiangfan Battery Separator Co., Ltd.:
“The Siveco maintenance consultant is not one who comes with a beautiful tie and a leather case… He prefers to wear working clothes like all the other maintenance workers. When his technical assistance is needed, he is personally involved in repairs, troubleshooting and machine modifications. He isn’t afraid to get dirty to solve technical problems. When the Siveco consultant is not at his desk, you will sure find him somewhere in the plant!”