Digitalizing O&M management at Baosteel Gases plants with EMM and bluebee®
The EMM team of Baosteel Gases won the 2016 Prize for Outstanding Contribution by Baosteel Science and Technology Association for this project.
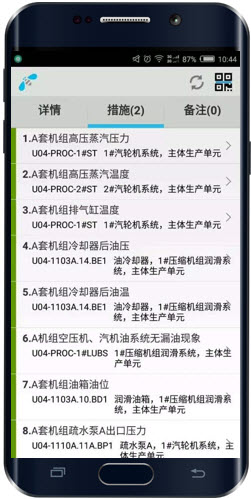
The author of this paper is Yan Wei, Operation Director at Baosteel Gases.
China’s leading industrial gases company, Baosteel Gases is affiliated to Baosteel Metal, a wholly-owned subsidiary of Baosteel Group. The five strategic business areas of Baosteel Gases are air separation, packaged gas, hydrogen, syngas and clean energy. It also integrates supporting competences of R&D, sales, logistics, construction and operation.
Following the EMM system (see case study of the EMM – Coswin 8i implementation at Baosteel Gases), the bluebee® inspection system was successfully put into use on August 29, 2017. Both are used to manage the maintenance and reliability of the plants, providing strong support for lean operations and closed-loop management. This project opened a new chapter in the digitalization of the plants’ maintenance management.
Baosteel Gases totally integrates Reliability and Maintenance in its management model and its daily work, in order to ensure the safe and stable operation of the plants and to provide high quality service to customers, through the EMM and bluebee® electronic patrol system. Based on an approval mechanism defined in the Core Model, the Preventive Maintenance and Inspection plans of each plant need to be reviewed by headquarters before being made available in the system. The EMM then automatically dispatches work orders to the operators’ bluebee® mobiles, to guide their inspection patrols, to facilitate problems identification and to ensure timely recording of text, photos or other information directly on the scene. Meanwhile, supervisors will receive and approve work orders in the EMM. A real-time “kanban” screen is available at the operation and maintenance office, so that supervisors can understand the situation in a timely manner and arrange appropriate teams for troubleshooting.
Baosteel Gases has developed a series of specific maintenance modules with the help of Siveco. One of them is the MOC (Management of Change) module. This module facilitates the submission by the plant of complete safety and technical plans for technical modifications. Resulting execution work orders are then followed by professional experts at headquarter, ensuring that new technical projects remain under control. Potential technical issues can be assessed and mitigation scenarios prepared.
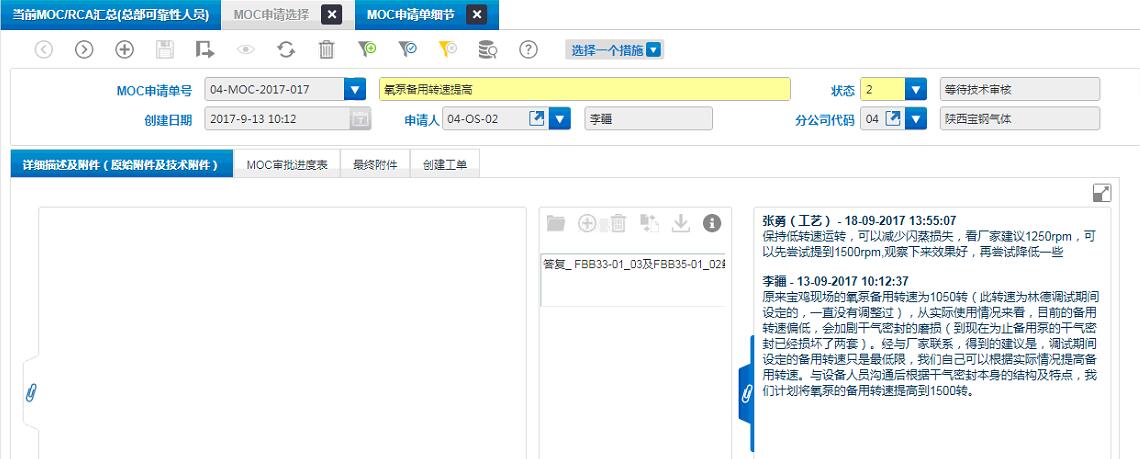
In the FMEA module, when reporting repair work, the engineer will record fault diagnosis (symptom, cause and solution for this specific equipment). Based on this data, the plant’s reliability engineer will be able to regularly compare his FMEA action plan with the actual equipment failures, thus improving the effectiveness of FMEA from practice. Through the continuous accumulation of failure data in the EMM system, engineers can also more accurately determine the cause of failure and quickly define the best solution for repair.
After the EMM system went live, Baosteel Gases’ reliability team continued to bring new requirements to the Siveco project team, based on system usage. Thanks to the flexible configuration tools provided by EMM, no software development was ever needed, saving both time and money. During the first year of usage, Baosteel Gases independently deployed the EMM to four plants, each with its own user interface and specific needs. The central team gathered suggestions from the plants and reasonable common demands were implemented, for example: repair orders may be directly assigned to a specific technician, but this information can be changed onsite if another person performs the work.
Apart from day-to-day maintenance management, another major highlight of the EMM system is the use of standard reports to analyze maintenance on a monthly basis, from different perspectives: equipment, work, time and others. The system displays visual Key Performance Indicators to help the plant management team gain an intuitive understanding of current equipment maintenance, for example: top ten equipment items in terms of cost, labor, average down time, etc. On the other hand, headquarters manager can obtain macro-level data for benchmarking, for example a comparison across all plants of work completion ratio, inspection completion ratio, preventive plan on-time execution ratio, etc.
The plants and headquarters can query reports at any time, but users also automatically receive reports from the system, on a regular basis, according to their role in the organization. For example plant shift leaders receive a report showing the previous day’s exception records (measurements outside normal range, abnormal inspection results, safety issues…); headquarters’ managers receive a summary report for all plants.
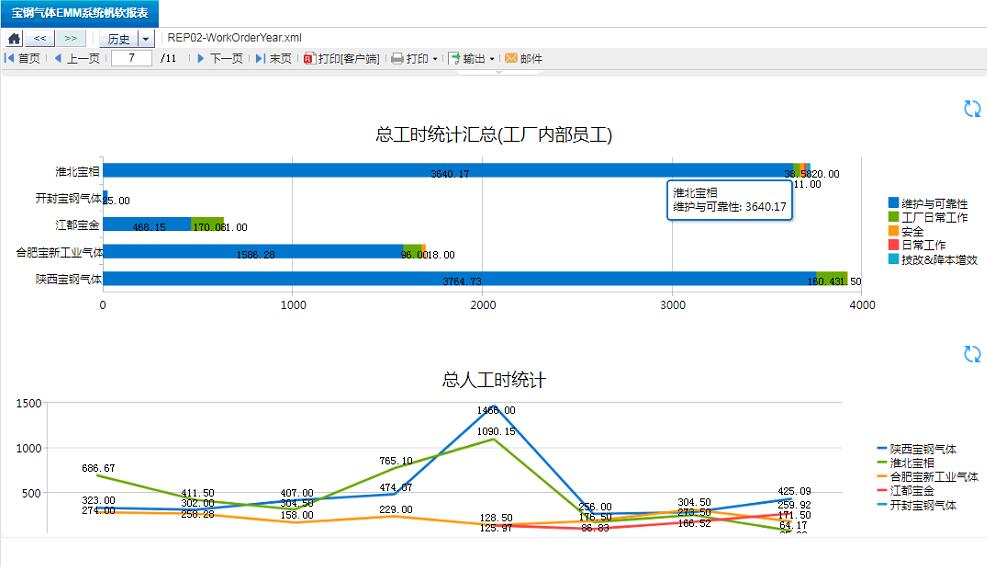
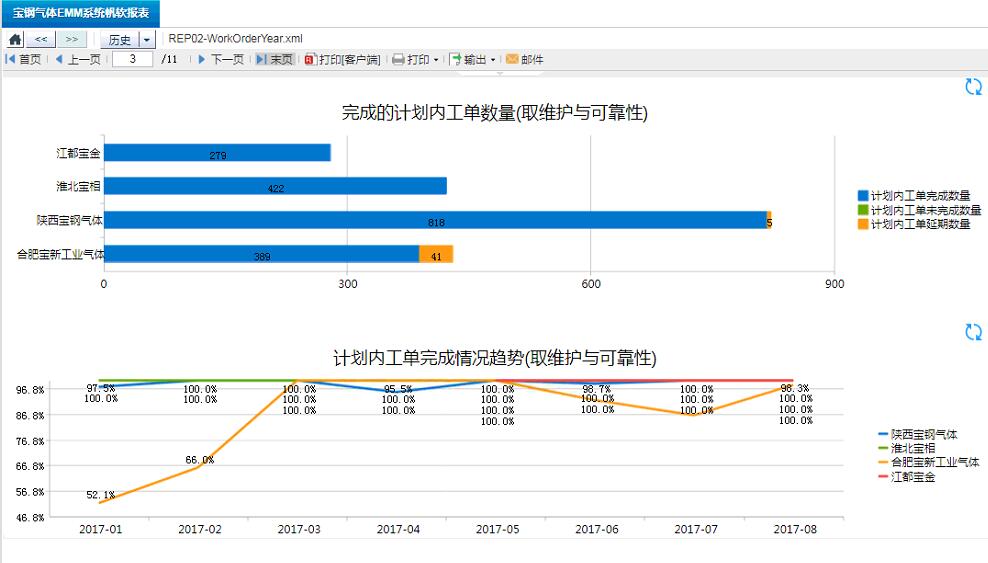
After a year of preliminary research, system implementation, commissioning and other preparatory work, Baosteel Gases electronic patrol system (bluebee®) was successfully put online at Shaanxi Baosteel Gases plant. The EMM, combined with the electronic patrol system, has now completely replaced the old-style paper-based management, low-quality and low-efficiency; information islands have been eliminated; the goal of digitalizing plant operation and maintenance has been realized.
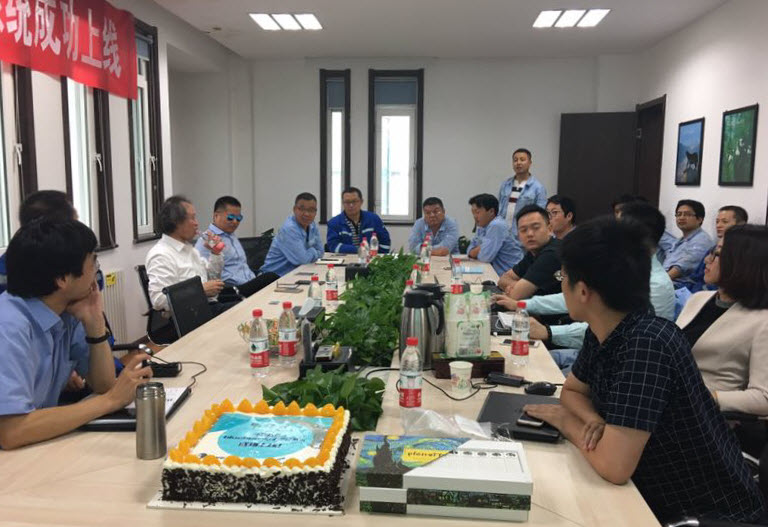
Party for bluebee® going live at Baosteel Gases plant