Maintenance 4.0 in practice: optimizing water supply assets with field inspections on mobiles
This project was nominated for the 2015 SFW Innovation Trophies.
Chongqing Sino French Water Supply Company Limited
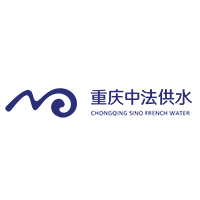
Chongqing Sino French Water Supply Company (www.cqsf.com.cn) is a joint-venture of Chongqing Water Group and Sino French Water, supplying drinking water to 1.2 million people. Chongqing is China’s youngest municipality under the jurisdiction of the central government and the gateway to Western China. This JV was the first concession project following the opening up of China’s distribution networks to foreign involvement and also Sino French Water’s first large full services venture in China. In operation since November 2002, the JV remains the sole drinking water supplier and network manager for Jiangbei, Yubei and the new developed zone in the Northern part of Chongqing. This area is developing quickly and, over the past years, the demand for water has grown at an average rate of 14% per annum. In 2009, the JV also secured a new drinking water distribution contract for Yuelai District, with a daily capacity of 600,000 m3, representing a total investment of RMB1.5 billion.
The project
To meet its maintenance improvement objectives, Chongqing Sino French Water has implemented the Coswin computerized maintenance management system since the beginning of 2013, covering the operation of 4 subsidiary plants. By getting rid of its old-time Excel-based management model, the project helped Chongqing Sino French Water build up a complete technical database and to streamline its previous preventive maintenance plans and fault reporting system, while optimizing decision-making through reports and KPIs generated by the system.
After one-year operating with the system and the results obtained, new requirements were raised by the management team: based on the CMMS, how to fill in the gap between onsite inspection and back-office engineering? How to replace the current paperwork by state-of-art technology? How to implement the best maintenance practices in the field? How to analysis the performance of inspection? How to motivate the junior technicians?
Inspired by the concept of “Maintenance 4.0”, Chongqing Sino French Water was determined to use advanced mobility tool to improve the inspection work.
The goals
Based on initial studies, the project aimed at achieving the following objectives:
–
Link the existing Work Orders (WO), preventive maintenance plan and fault codes (SDCA Symptom, Defect, Cause, Action) from the CMMS to onsite users and data, in order to bridge the gap
–
Streamline the inspection SOP based on ISO 55000 and set up a comprehensive inspection technical database to prevent mistakes in the field
–
Use technology to guide end-users to follow the best practices while improving work safety
–
Analysis inspection results to provide technical-financial decision support
–
Motivate the staff by fancy technologies, becoming the benchmark among all the Sino French JVs
The solution
Chongqing Sino French Water decided to work with Siveco to implement bluebee® solution to meet its inspection needs. bluebee® is an off-the-shelf, well-proven Maintenance 4.0 software package, unlike most self-developed applications found in the market. The coverage of the project included the 4 subsidiary plants and 30 pumping stations in the water supply network. The project required 46 mobiles phones (20 for plant maintenance, 24 for inspection and the rest for pump stations) and 1,200 QR-coded tags corresponding to 1,200 inspection areas. The total number of people using bluebee® is 88. The project started in January 2015.
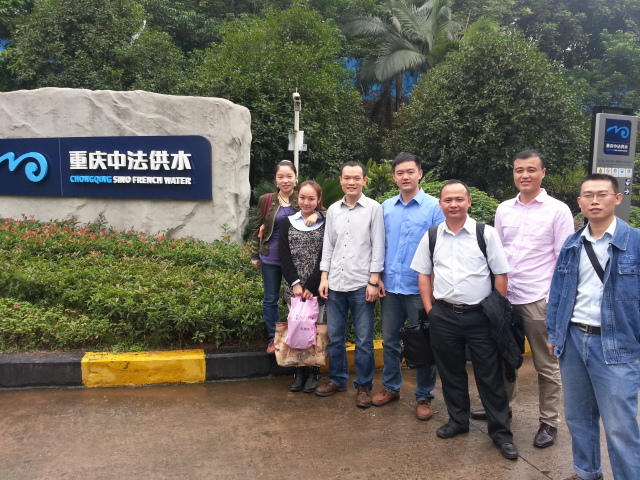
The joint project team
To reach World Class Maintenance, the new inspection process was defined based on ISO 55000 Asset management, involving inspection strategy and policy, organization, equipment coding, job coding, job description, job type, job frequency, actions, action types, scan QR codes etc. Measurements were standardized as well in terms of temperature, vibration, pressure and normal values were defined. This was documented in the “Core Model”.
Beyond traditional inspection tools, the bluebee® app allows users to create Work Orders and Job Requests once a problem is detected onsite. The technical know-how database is made available to field users for diagnosis and decision support. Through 4G network, the mobile phones can automatically synchronize data with the Coswin back-office system.
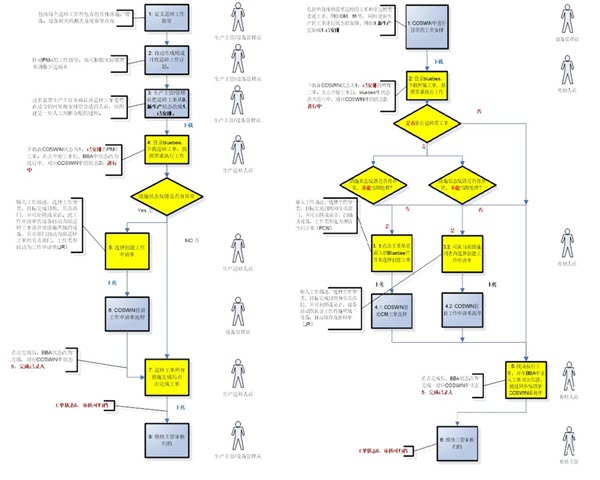
Left: production inspection, right: maintenance inspection
The Core Model established above has been adopted and configured by Siveco into the app. Considering the complex working environment and existing working habits, the user interface also ran several tests to ensure the smooth hand-over. The project officially went live in August 2015.
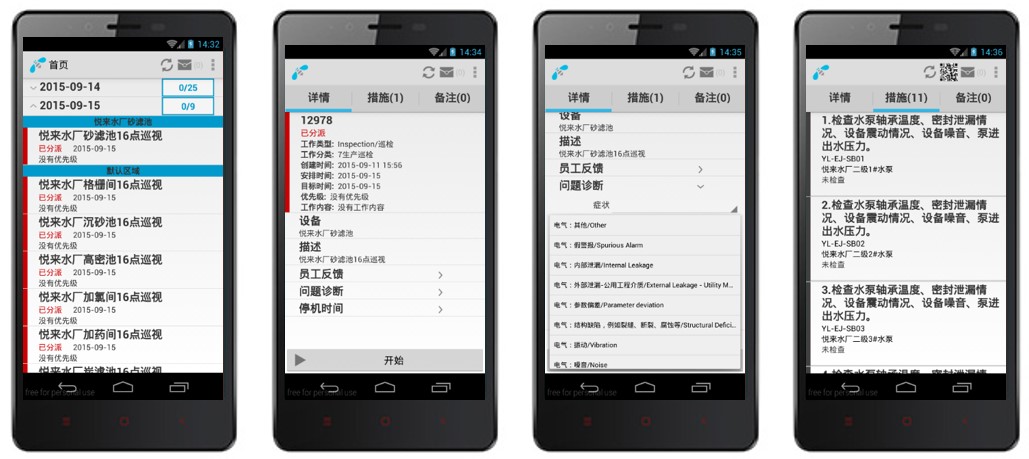
bluebee® app: WO list, WO, diagnosis, action list
End users training
The benefits
In short term, Chongqing Sino French has defined certain reports and KPIs to measure the results and progress compared to the previous management model:
Measurements over safe value
Meters trends
Abnormal failures analysis
Comprehensive inspection analysis
Unfinished job analysis
Meters trends
Abnormal failures analysis
Comprehensive inspection analysis
Unfinished job analysis
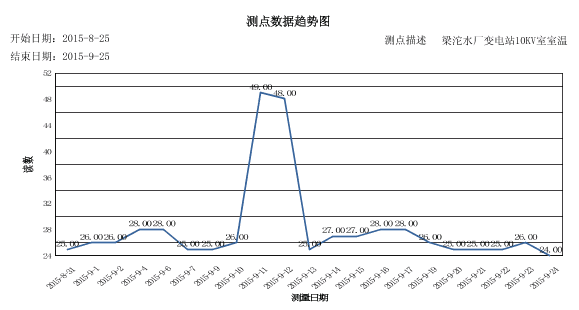
Sample meter trend report from the Liangtuo plant
The bluebee® project improves the field inspection through SOP and systematic analysis. One stone, two birds: it also optimizes the usage of the existing CMMS system, ensuring greater ROI. The project also contributes to higher safety, always the top priority for Sino French Water.
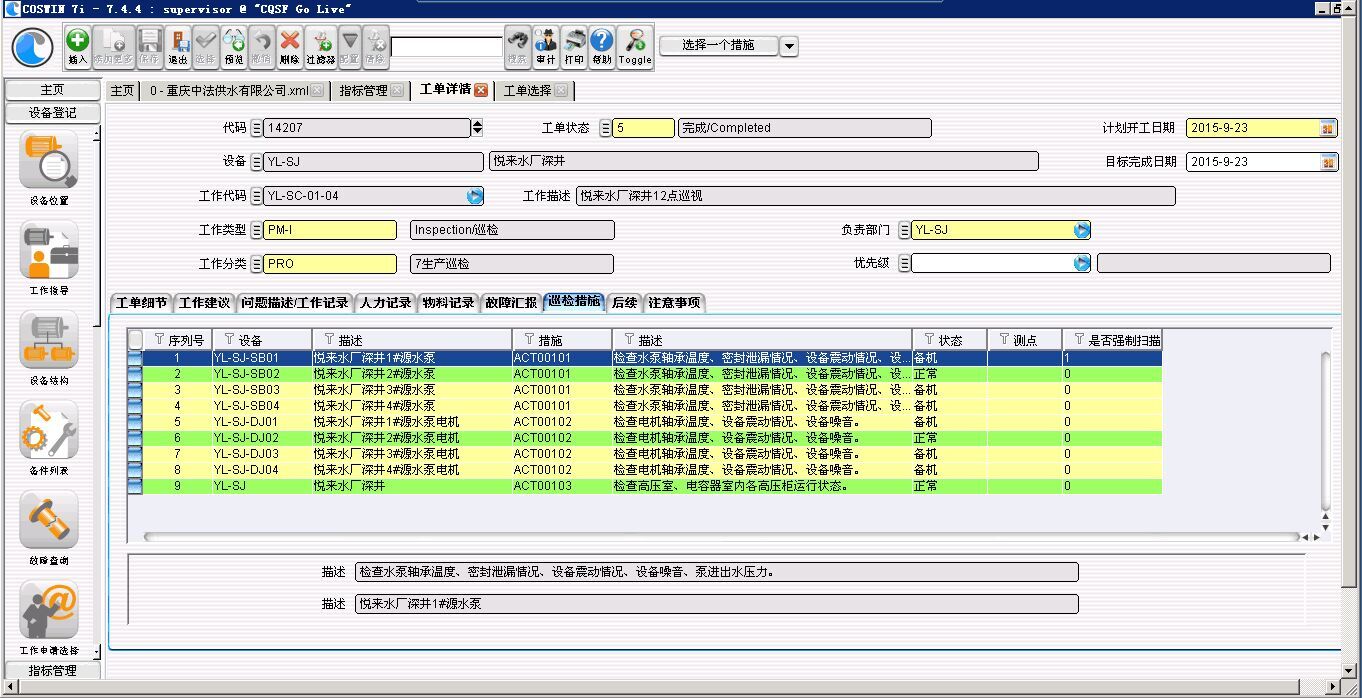
Inspection work order shown in the Coswin system
According to Wang Zhibing, Chongqing Sino French Water’s Production Leader: ”We got rid of pen and paper and it is fun to be equipped with bluebee® while working. ”
Luo Feng, the company’s Operation Manager, added: “The bluebee® project improves our inspection process, while ensuring the safety of our operations.”
The introduction of “Maintenance 4.0” and more generally “Industry 4.0”, corresponds to the “New Normal” phase of China’s development. It requires the combination between new Internet technologies and industrial know-how. As a pioneer, Chongqing Sino French Water took the first steps to adopt this concept into day-to-day practice. The project not only motivated workers but also demonstrated the value of their work and their capacity for innovation.
Based on the complete inspection Core Model established in Chonqging, bluebee® is planned to be duplicated to the other Sino French Water JVs in 2016.