Operational Excellence & Continuous Improvement: Baosteel Gases Excellence Maintenance Management (EMM) system goes on-line
This article was first published in Baosteel Metal magazine “VISION” P7-10 (available here for download). Author: Chen Yi, Baosteel Gases.
In April 2016, Baosteel Gases selected Siveco’s Coswin 8i for their Excellent Maintenance Management System (EMMS) project, aimed at strengthening the company’s reliability and maintenance excellence program. Its first phase, to establish a maintenance “core model” with guidelines applicable to all sites, was completed in June. The system went live on the first pilot site in July (see News).
At the end of July, after about a year of careful preparation, Baosteel Gases’ Excellence Maintenance Management System (EMM) was officially put into use in the first pilot plant of Hefei Baoxin Gas. This event marked the transition of Baosteel Gases ASU (Air Separation Unit) business from a paper-based disparate management approach to a computerized and standardized management system.

Baosteel Gases initially established its “Operational Excellence & Continuous Improvement” concept to ensure high reliability and stability in plants operation. However, to more effectively achieve this goal, a management system or platform was needed to support and promote the concept. This is especially true for Baosteel Gase, with its “headquarters + subsidiaries plant” model: how to ensure its execution, implementation, feedback in the daily management and operation of the various subsidiaries? Based on this, Baosteel Gases began to deploy the EMM system.
Nowadays, advanced, large-scale companies at home and abroad, all have their own customized management system, SAP or CMMS systems. Its main purpose is to standardize and solidify the company’s daily operation and maintenance process, rather than staying with paper-based management. Over time, large amounts of operational data accumulate, also known as “Big Data”, enabling a PDCA feedback loop and long-term optimization, to ultimately achieve high reliability.
Baosteel Gases EMM system
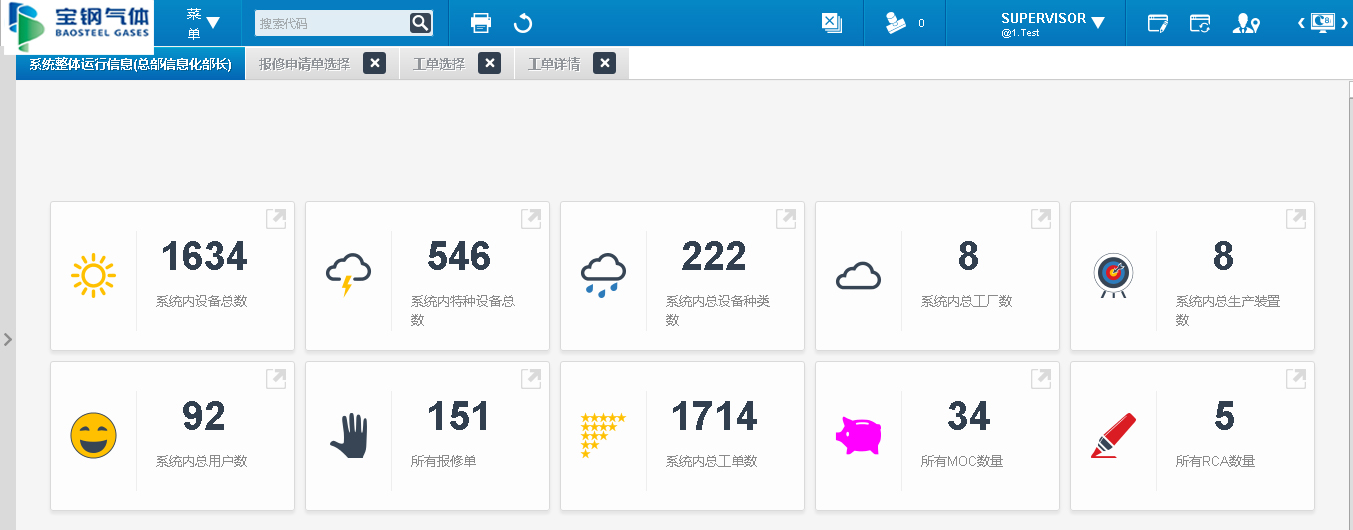
Based on the PDCA feedback loop concept, Baosteel Gases EMM system is currently composed of 5 modules:
Standardized equipment database: standardized equipment hierarchy, equipment types and their main components, equipment, technical specifications and preventive maintenance work libraries.
Workflow and reporting: daily routine management processes and tracking, daily preventive maintenance work order processes, and various associated KPI data reports.
FMEA (Failure Mode and Effect Analysis): components failure mode analysis, management of equipment types and components, and the actual management of the fault analysis process.
MOC (Management of Change): management of plant and equipment modifications, approval process for changes, and the associated equipment database.
RCA (Root Cause Analysis): handling and tracking of root cause analysis procedures for failures, and the associated technical database.
Overall design of the EMM system
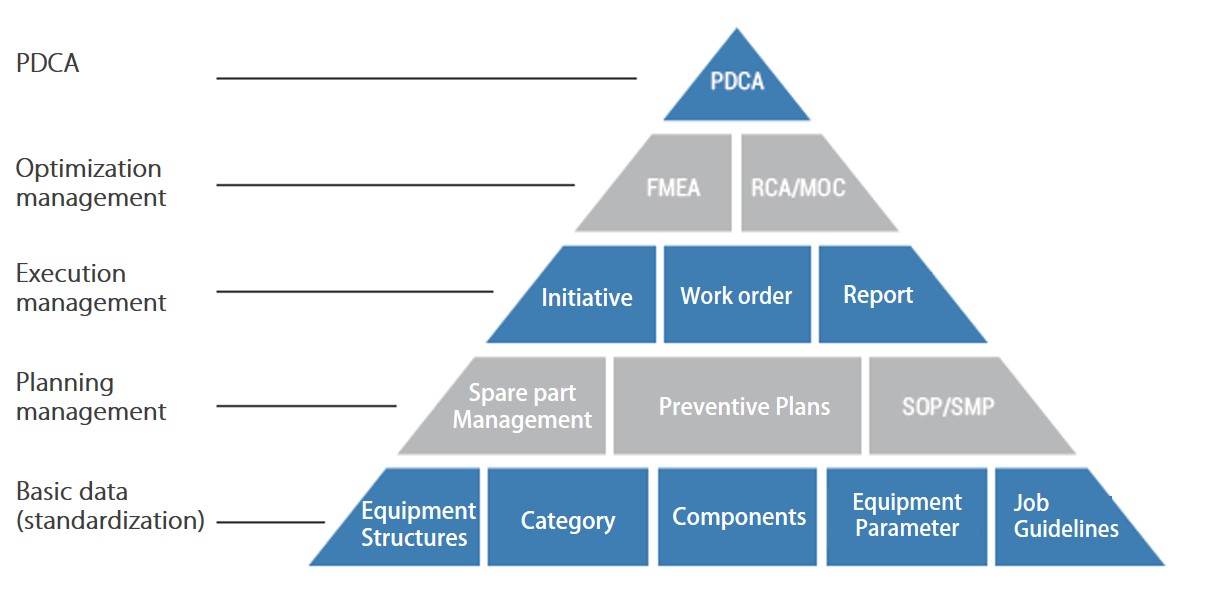
Baosteel Gases EMM innovation
Innovative integration of management tools: at present large domestic and multinational companies utilize CMMS, RCA, FMEA and MOC tools, but those are usually separate software packages. Baosteel Gases’ EMM system, on the other hand, took all tools and functionalities into consideration from the design stage, realizing them in one single platform rather than separate systems, providing comprehensive data support for the group’s overall management and optimization.
Standard FMEA for equipment categories and components: while most of plants in China perform FMEA at equipment level, Baosteel Gases does it more accurately at main component level. The theoretical FMEA is linked to the actual fault diagnostics (PDCA module) in work orders, thus the actual diagnostics can validate the FMEA definition and help improve it.
Innovative standardization: Baosteel Gases ASU division operation team carried out extensive work, reviewing and analyzing the current daily operation and maintenance practices, preparing a unified standard applicable to the various subsidiaries, standardizing data preparation requirements, such as equipment types, technical parameters, etc. Finally, maintenance processes were standardized in order to facilitate unified, advanced, practices for both old and new plants.
Group deployment: Baosteel Gases considered group deployment from the inception of the project, unlike traditional site-by-site deployment, taking advantage of Big Data analysis and standardized management to smoothly promote the project.
Benefits for Baosteel Gases operations
– Clarify work in the plant: we often wonder why some of the company’s employees are very clear about what to do, how to do, why do it, with a strong sense of initiative. Through careful observation and analysis of the best companies, you can identify a basic management system driving behaviors and processes.
With Baosteel Gases EMM on line, the maintenance staff, daily, weekly, monthly, annual preventive maintenance work is immediately visible: “Who does, how to do, when to do.” For operators, work orders, MOC and RCA guide the operation and management processes and their daily tasks.
For plant managers, since most of the work has been standardized and clarified, it is now possible to focus on the major aspects of the plant:
1. Plant annual maintenance budget and spare parts procurement plan: thanks to the preventive maintenance plan, most of the work to be done at the plant each year is defined, with corresponding costs and spare parts requirements, resulting in an accurate plant maintenance budget. The spare parts procurement plan will also be of great help.
2. Track and control incidents in a timely manner: thanks to the fault reporting and RCA process, the causes of each incident are systematically analyzed, ultimately ensuring safe, stable and efficient plant operation.
3. Management and control of plant technical changes: with the MOC approval process managed in the EMM system, there will be a comprehensive support from headquarters, taking safety and cost into consideration, as well as the early technical program review and late document compliance and drawings updated.
– Data and experience sharing: all Baosteel Gases plants use the EMM system and this data is open and shared, so that staff from any plant can view the other sites data and experience, so as to optimize plant operation and maintenance.
– Continuously improve operation and maintenance of both new and old plants: For older plants where the management system is imperfect based on existing habits, continuous improvement is a complex task. The EMM system now in place to promote change is conducive to rapid improvement in management level. For new plants, this standardized, shared management platform helps setup the management system quickly and comprehensively to achieve a multiplier effect.
– Big Data for operation and maintenance: the EMM system aggregates and analyses actual data from all Baosteel Gases subsidiaries, providing objective basis for decision-making and management at headquarters level.
For example, system data may show that a certain manufacturer’s equipment has high failure rate and poor reliability. Related data analysis can be sent to the procurement and engineering departments in order to optimize future projects, thus reducing operation and maintenance costs. In another example, a particular brand of equipment experiences safety problems in one of the plant: through the system, all machines of the same type can be identified across all sites and all plants concerned be notified, thus preventing a safety risk.
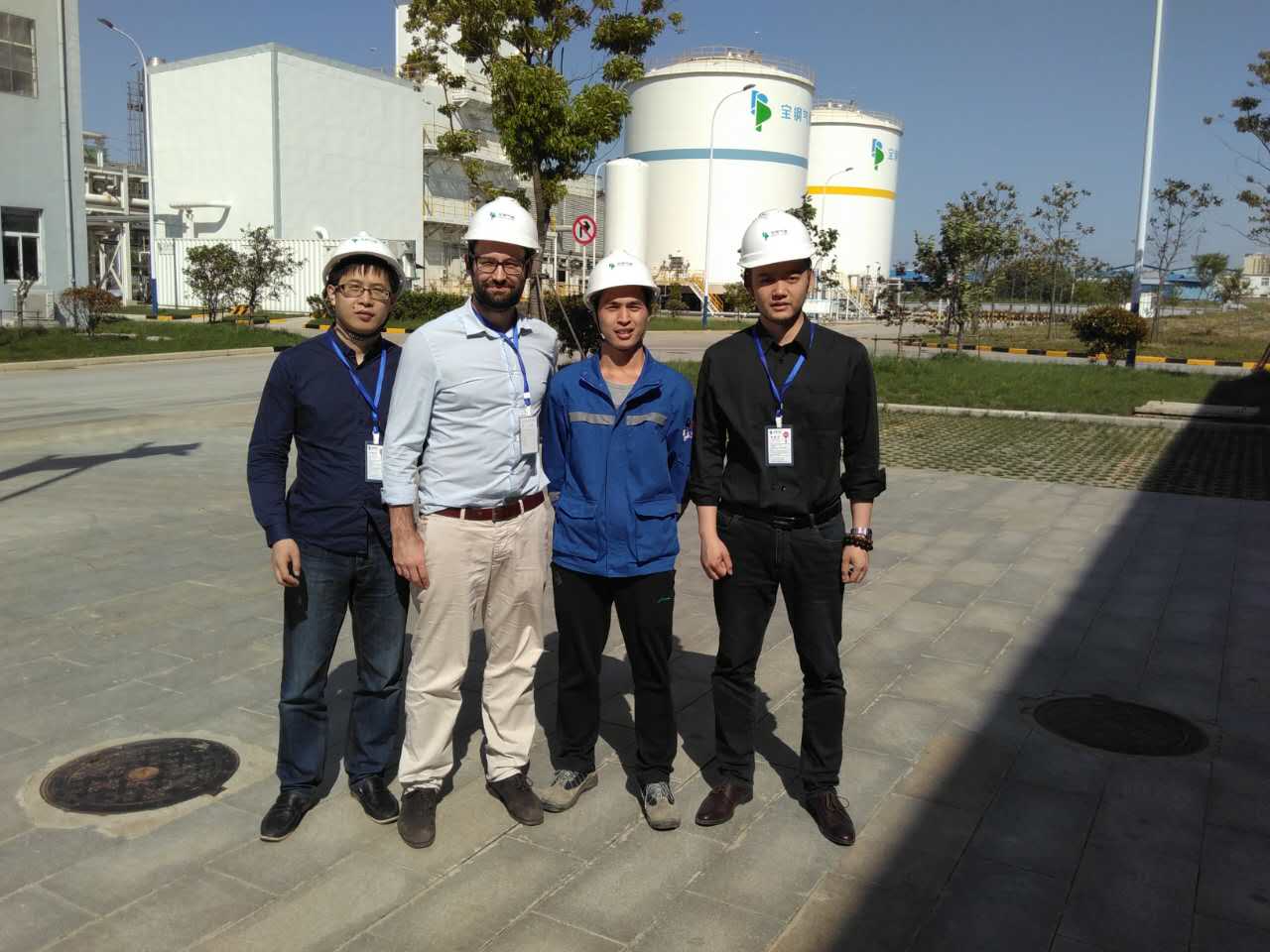
Building the Baosteel Gases’ EMM
For multi-site companies that want to launch a new maintenance management system, top-level design and planning need to be carefully considered: how to define the standard database, how to design workflows that match daily operations, how to build a preventive maintenance plan, how to set KPIs, how to extend the system in the future, how to strike the right balance between functional depth and ease-of-use, and how to manage headquarters standards and SOP / SMP files, etc. To achieve this, Baosteel Gases’ operation team at headquarters conducted an extensive implementation study and business process review.
The purpose of project was to solidify all the management file and processes into the management platform. Information Technology is used to ensure that work execution is compliant with standard, with all feedback data stored in the system. The management team is now able to optimize processes and standards by analyzing the data. Thanks to this PDCA approach, efficiency, safety and reliability of plants operation is continuously improved.