The implementation of ISO 55000 and Maintenance 4.0 at Capital Water
The author Wang Guanghui is General Manager of the Operation Department at Capital Water Group.
Beijing Capital Co., Ltd. was established in 1999 and listed on the Shanghai Stock Exchange in April 2000 (SH60008). As a professional water service provider, the company has made significant achievements over the years:
- The world’s 5th largest water operator
- The 1st state-owned listed enterprise in the environmental protection area
- The 1st listed company to invest in commercial water supply and the first state-owned company to introduce Public-Private Partnerships (PPP) in the water industry
- The most experienced water company in China with the highest water supply capacity
- The largest and most experienced enterprise in the field of rural sewage treatment
- Top 10 influential enterprises in China’s water industry for 15 consecutive years
- The 5th most influential enterprise in China’s solid waste industry for 2 years in a row
- The 1st state-owned listed enterprise in the environmental protection area
- The 1st listed company to invest in commercial water supply and the first state-owned company to introduce Public-Private Partnerships (PPP) in the water industry
- The most experienced water company in China with the highest water supply capacity
- The largest and most experienced enterprise in the field of rural sewage treatment
- Top 10 influential enterprises in China’s water industry for 15 consecutive years
- The 5th most influential enterprise in China’s solid waste industry for 2 years in a row
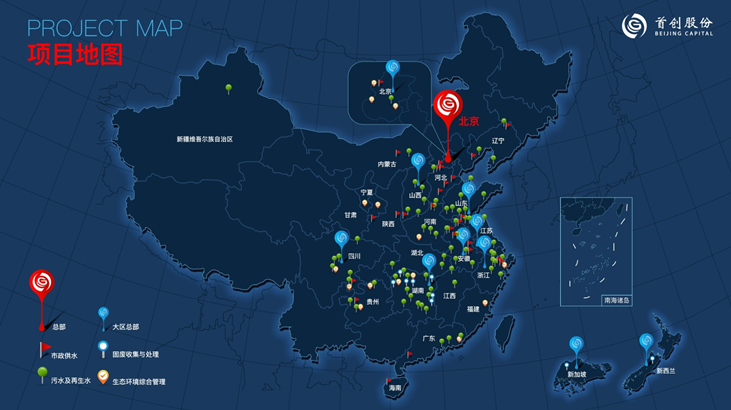
Introduction
In October last year, after in-depth exchanges between the two companies, we found that Capital Water and Siveco China, the pioneer of “Maintenance 4.0”, shared common goals and expectations in terms of maintenance improvement. Therefore, we launched our company’s Asset Management system, based on the advanced management concepts provided by Siveco and the ISO 55000 international standard, applied to the company’s specific situation, in order to further enhance Capital Group’s reliable service to municipalities across China.
Through this cooperation with Siveco, we aim to set a new benchmark for maintenance management in the Chinese water industry, ensuring public safety, sustainability and optimizing life-cycle cost by developing a systematic approach to asset management and enforce it across all our companies.
As a result of the project, a Group Core Model was created by the joint project team of Capital Water and Siveco China in compliance with ISO 55000 and its Chinese equivalent GB/T 33172, while also taking into account our company’s and our Chinese market characteristics.
The Group Core Model provides a strong framework for all stakeholders for at group level and site level. Furthermore, it contains practical guidelines for defining maintenance work processes, management and analysis reports, key performance metrics, etc.
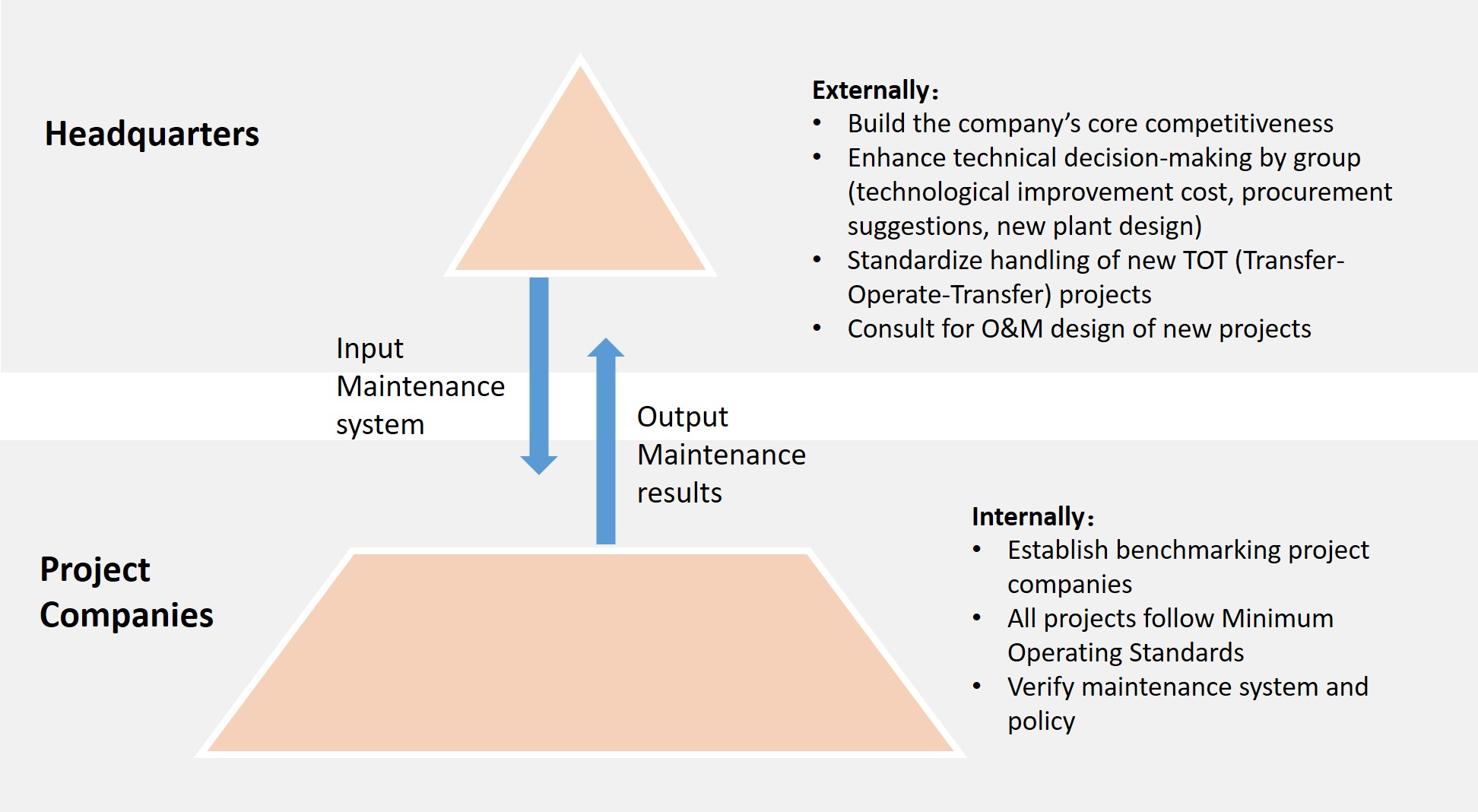
One maintenance policy, nine objectives, five steps
A maintenance policy was defined, with nine objectives for its implementation, fully in line with our company’s strategic objectives. To attain these objectives, a five-step plan was then established. This five-step plan can be summarized as follows:
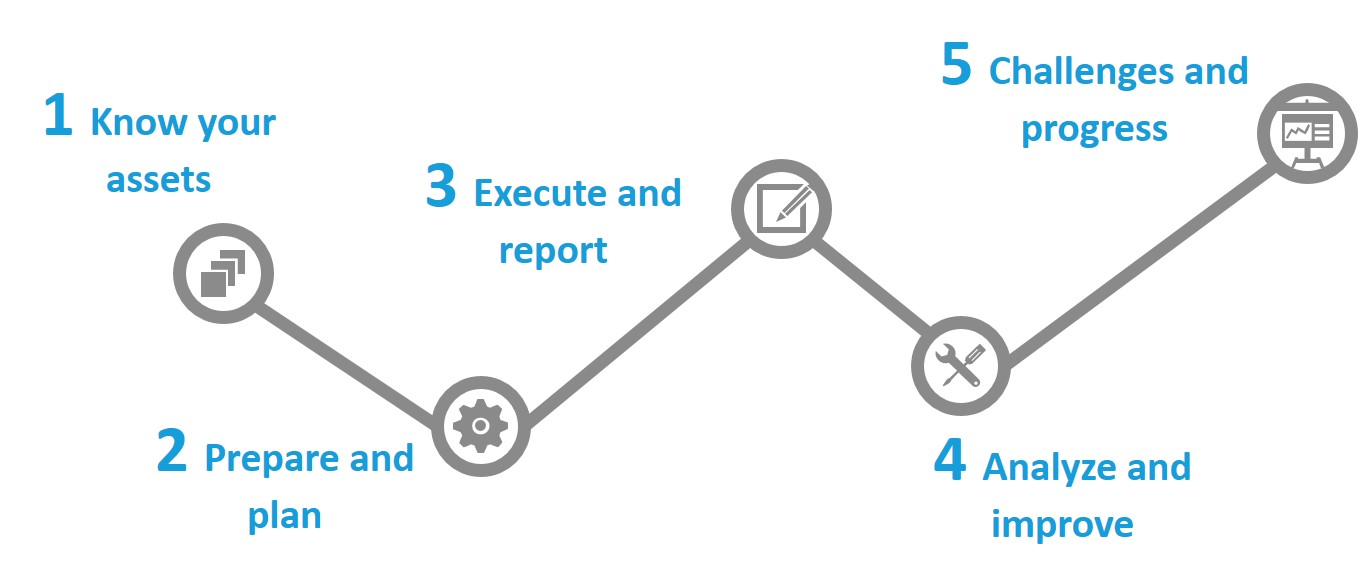
Step 1: Know the assets, establish a reliable asset register (asset code, name, classification, document, structure and asset’s critical rating); identifying each asset is the backbone for reliability improvement of Capital Water.
Step 2: Prepare and plan, define the asset maintenance plan and translate it into maintenance guidelines to implement the best practices and to achieve asset performance.
Step 3: Execute and report, ensure feedback using Work Orders for continuous improvement in asset management.
Step 4: Analyze and improve, rigorously review and analyze results to help the senior leadership of the company to formulate reasonable maintenance decisions to achieve the goals of asset management improvement.
Finally, in step 5: Challenge and progress, obtain sustainable improvement based on objectives; develop new benchmarks and strategies under the leadership of senior management.
Deploying the program into practice
In order to successfully deploy and achieve the goal of asset management in practice, the 5 steps of asset management need to be driven in parallel.
These drivers include roles and responsibilities of employees, communication and training, periodic meetings and audits, information system and documentation. The use of maintenance technology and maintenance management solutions in particular is critical to effectively support all the steps and to manage such large amounts of information, in fact “Big Data”.
The first deployment is currently ongoing at a pilot company, Yuyao Water, using Siveco’s Maintenance 4.0 solutions (central database Coswin 8i and bluebee® mobile for operation and maintenance inspections).
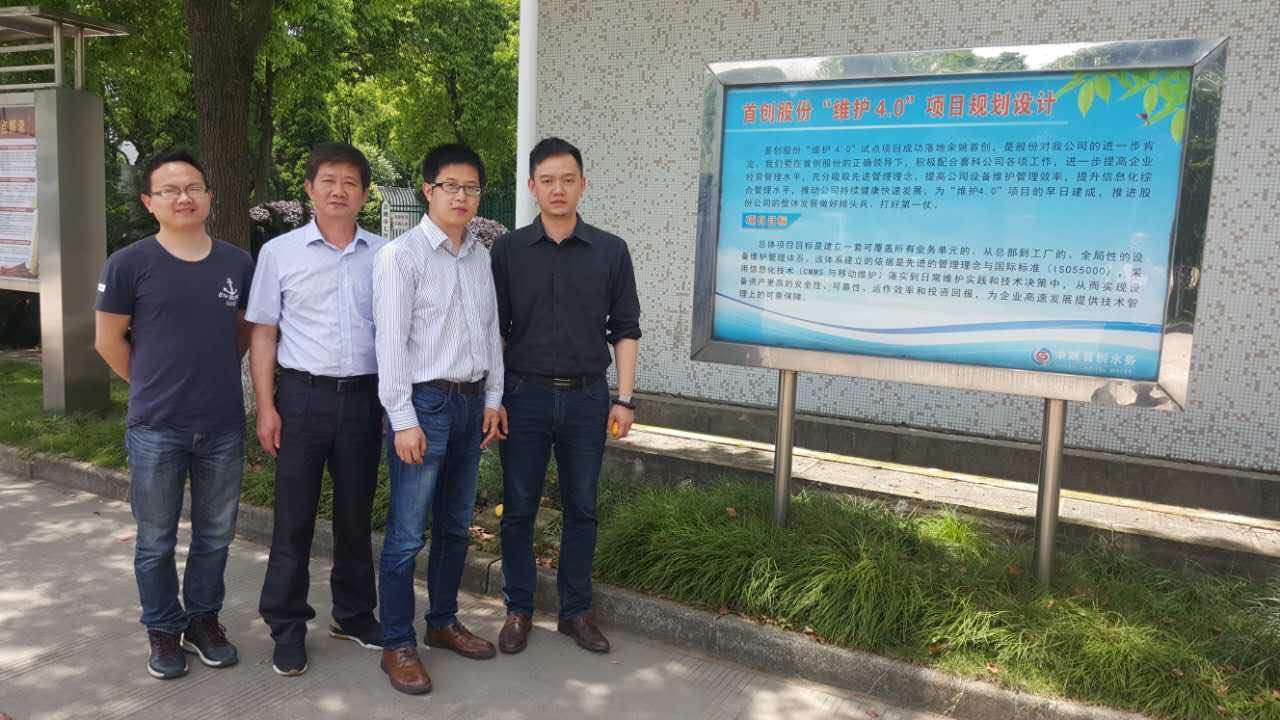
Picture of the joint team at Yuyao Capital Water