Maintenance improvement in the coronavirus times
Dear Reader,
For two months already in China we have battled the coronavirus. Or rather, workers at the forefront have battled the virus, while we have only played our role as good citizens. As the crisis has continued to spread, our friends all over the world now face the same challenges and suffering, striving to overcome it together. With all the talk about remote work, working from home, videoconferencing, it cannot be forgotten that all vital services rely on people physically working: from farmers to factory workers producing essential equipment, technicians maintaining infrastructures providing drinking water, waste management, electricity…
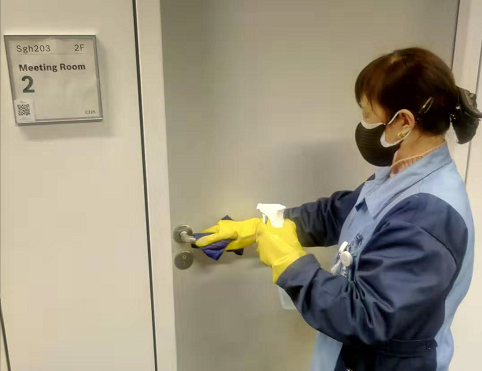
GSN use bluebee® for WeChat to record all disinfection work during the crisis
Many of our clients have taken advantage of this special time to reinforce their management. Digitalization is high on the agenda, as it has proven a powerful ally against the epidemic. Many companies have also identified maintenance (and its close relatives, risk management, HSE, inspections), as priority areas to improve, in order to emerge stronger from the crisis. In our previous newsletter we have shared some of these stories and we will continue to promote special services to assist our clients. In this month’s newsletter, we want to share some of our experience in the manufacturing industry, taking the example of the aerospace manufacturers, with their stringent regulatory and quality requirements.
Siveco is better known in Asia for our track record in public energy and environment infrastructures, with many large-scale multi-site state-owned clients running Smart O&M programs to optimize their core business, but we also have a significant number of manufacturing clients. Some of our Chinese manufacturing customers in particular have been showcased for their Maintenance 4.0 solutions and have received attention from leading multinationals as well (example of Baosteel Packaging, features in one of our movie case studies). Manufacturers are often preoccupied with short-term costs reductions. In the past few years, many of them have initiated large Smart Manufacturing projects. We observe that, more and more, such projects are being challenged, sometimes stopped, due to high cost and long implementation periods, sometimes several years. In a sense, the crisis offers opportunities to redirect, to streamline, those digitalization projects to achieve quick returns. Maintenance is often the low-hanging fruit, never optimized before. We will explore some of these topics in this newsletter.
Over the years we have kept close relationship with our sister company Siveco Italy. In this month’s Customer story, we have chosen to share an article about leading aerospace manufacturer Leonardo and their predictive maintenance program enabled by our Smart O&M solutions. Our Italian colleagues, at the forefront of Maintenance 4.0 in their market, remain close to our heart during the COVID-19 crisis.
Our Partner article features TB Solutions, our consulting partner located in Taiwan, providing in-depth domain expertise in the aerospace market and covering the entire Asia region to develop aerospace clients with Siveco. In particular, we together target the most forward-looking companies that will take advantage of this crisis to streamline their 4.0 program in order to derive more practical and short-term benefits.
Finally, the Siveco people article shares the experience of some of our team members in the early days of the novel coronavirus crisis.
We hope you enjoy this issue, let’s overcome the crisis together, Siveco will support you!
Bruno Lhopiteau
Managing Director
Siveco China
Managing Director
Siveco China