Online annual assessments from Siveco support team
Since the beginning of 2020, the COVID-19 crisis has brought unprecedented challenges to our clients in China and all over the world. During the epidemic, the Siveco support team’s focus has been to care for the operation of each customer and their special needs. Under Siveco’s Enhanced Maintenance Support Contract (EMS), Siveco support team will visit customers’ site and conduct on-site assessments, evaluate their asset maintenance management this year and give recommendation and improvement proposals for the future. In this context of travel restrictions, on-site visits being impossible, the Siveco support team has already completed three annual assessments through remote meetings in April.
From April 13 to 15, the Siveco support team held its annual assessment with Hanas New Energy. During the meetings, both sides exchanged views on how to orderly achieve operation and maintenance work under the “safety first” rule, which remains the top priority for Hanas. To achieve new needs, Siveco team also introduced bluebee® mobile solution to Hanas team, which showed great interest in this easy-use and paperless solution and discussed its future implementation in the LNG plant.
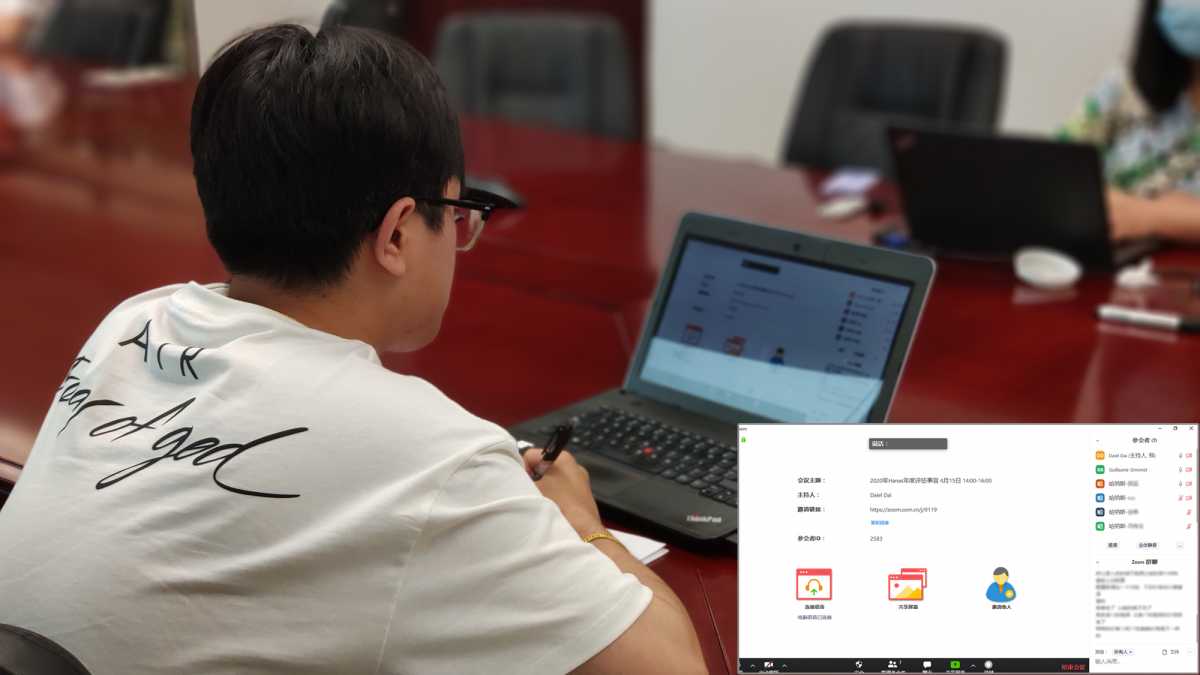
From April 23 to 24, the annual assessment for Saint-Gobain Maanshan took place. Siveco gave a comprehensive evaluation and analysis of the overall use of Coswin with Saint-Gobain Maanshan maintenance team. Compared to last year, the overall asset maintenance status of the factory has improved significantly. Both sides reached a unified opinion on next year’s maintenance improvement plan, which will play a great role in boosting the organization and technical improvement, and supporting best maintenance management practices in the future.
On April 28 to 29, the annual assessment of Taixing Suez Waste Treatment plant was held. The Taixing site started to use Siveco’s Smart O&M solution from the plant startup, which enabled the standardization of all work processes, full traceability of operation and maintenance, in order to achieve the plant’s availability target. During the meeting, two teams exchanged views on the use and optimization of the system based on user’s experience so far, with conclusions that lay a good foundation for next year’s maintenance improvement. Siveco also demonstrated the usage of bluebee® in similar Waste-to-Energy plants and in other Suez sites, which raised great interest from Taixing’s side to ensure accuracy and traceability of work.
Compared with on-site assessments, remote sessions obviously lack direct personal communication and interaction with the customers’ team, but both Siveco support teams and clients’ remain passionate about their work and keep good spirits. During the crisis, conference calls have of course gained popularity and by now everyone is used to such meetings, which helps with communication.
This experience with remote assessment proves that we can have heated and in-depth discussions with our customers on complex topics, performance, improvement methods, system usage, and that everyone remains earnest and friendly. We thank all customers who participated in these Siveco online assessment meetings! The Siveco support team will continue to support our customers with enthusiasm and best service! There is still a long way to go in the fight against the epidemic: may we work together to overcome difficulties and forge ahead!