Avoiding pitfalls when implementing TPM in China
Companies trying to implement TPM in China, usually as a part of a corporate roll-out, face specific challenges, which may differ from those observed in Japan or in the West, more developed economies where those initiatives, or the consultants involved, often originate from.
Maintenance jobs performed by operators, known as “autonomous maintenance”, and more generally the involvement of production staff in the improvement process are one of the key principles of TPM. One of the benefits of a successful TPM program would be to help operators acquire more responsibility, starting with simple jobs such as daily cleaning rounds, lubrication, bolts tightening and various checks. To those daily care routines, other activities are later added, such as the proactive tagging, directly on the equipment, of problems detected by operators during inspections – an excellent tool to visualize poor maintenance and its consequences. The final step consists in involving production teams in analysis and improvement sessions, from which the actual benefits of TPM will derive.
This article will look at some of the Chinese specificities that influence the TPM process, as observed in many projects conducted by Siveco, so as to help industrial managers avoid some the pitfalls.
Understanding HR limitations
The key words for autonomous maintenance may be: involvement, responsibility, and pro-activity – all which may be considered at odds with the HR situation in most companies… The challenge of trying to change old habits is obvious, although not unique to China. Specific obstacles exist, however, that make it more difficult for production workers to play their role in the TPM process, i.e. to share their experience and know-how of the machines. More often than not, in China, workers are not experienced enough: while they may have the theoretical knowledge in a specific discipline, the high turnover rate and lack of multidisciplinary skills makes it more difficult to gain mastery in their equipment.
Although there is no instant solution to this problem, we could state the obvious: plans should be put in place to reduce turnover and improve the skill level. The maintenance improvement plan itself, based on TPM or not, will greatly contribute to this (as noted in our article “A contrarian approach to maintenance”). In any case, these specific constraints should be kept in mind when rolling out a TPM program.
Reducing breakdown rate before TPM
Before launching autonomous maintenance activities, it is necessary to have the failure rate of the machines under control, and if possible relatively low. How to transfer first line maintenance responsibility to operators if the equipment is always breaking down? We often see maintenance technicians working full-time on emergency maintenance, always on the shop floor fixing machines: in such a situation, autonomous maintenance cannot be implemented (apart from cleaning and basic checks).
Instead, it may be preferable to stick with the traditional organization and to focus on reducing the failure rate through preventive maintenance. This is evidently true for aging facilities, making TPM naturally more applicable to new factories.
Implementing work feedback first
When transferring part of the maintenance job to production, the previous uniqueness of “memory” is lost: the maintenance department was once the unique depositor of all the plant knowledge, but now this knowledge is spread across the organization. Having a system in place to centralize the knowledge, based on work feedback, is critical. Without such a system, there is a significant risk that production and maintenance do not know what the other is doing. On one hand, a comprehensive maintenance record is a necessary tool for failure analysis (more on that in the next section). On the other hand, a work feedback system will allow, for example, maintenance technicians to know that a quick fix was applied by production operators, in all good faith, which may require further attention.
We recommend focusing on Work Order (sometimes also called Job Request) to capture the most essential information. This process can be greatly simplified using predefined check-lists: symptom, failure type, downtime (exact values may not even be needed, e.g. operators could choose between 5min, 30min, 2h, 4h, 8h+). Using Siveco’s mobile solution bluebee® this process becomes painless: employees are equipped with smartphones, take pictures of the problem, select the information needed and can receive troubleshooting help directly from a central database.
The most striking benefits from any maintenance management program, including TPM, will derive from the systematic analysis of historical records. Experience has proven that this can only be achieved with a CMMS: paper and Excel-based systems simply do not allow proper technical analysis over a period longer than a few weeks. Real measurable benefit will come from improvement decisions based on historical data.
Enabling maintenance improvement
Plant improvement can only be carried out if the maintenance team, freed of part of their workload (first-line maintenance now transferred to operators) is able to dedicate their efforts to it. When technicians were busy repairing the machines, this process could not take place. On the other hand, if technicians used to be lazying around in the workshop, TPM may not have been the right choice.
It is essential for maintenance workers to understand that they should now involve in, and be measured on, reliability improvement. This is not like in the old days, when they could sleep in the workshop waiting for the next breakdown.
The maintenance team has to be prepared for this change. More particularly, it should acquire some of the key methodologies and tools needed to perform their new work: root cause analysis, the design and implementation of preventive maintenance, etc. The basic reports and KPIs have to be in place (see Tips & Tricks article about OEE, the most emblematic KPI of TPM).
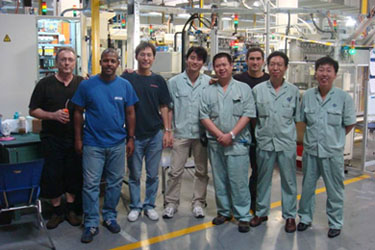
Joint team at ZF Shanghai Steering
In conclusion – a prerequisite to TPM
In conclusion, TPM can be implemented only when:
– The failure rate is stable and preferably low
– A work order system is in place
– The maintenance team is prepared to take up a new role dedicated to improvement
– A work order system is in place
– The maintenance team is prepared to take up a new role dedicated to improvement
While TPM has proven very successful in countries with a long industrial history, where maintenance engineers already had a strong methodological background, China brings its own specific challenges. It is our experience that a TPM initiative cannot succeed without those fundamentals – structure, methodologies and tools. Implementing a CMMS has proven to be the most efficient approach to create such a structure, in a sustainable manner, in China. This implementation will have to be done before or at the same time as TPM is introduced to the company. For more insights on the subject, interested readers may refer to the other article “A contrarian approach to maintenance”.