Achieving Better Risk Prevention in Chinese Terminals
This article was previously published in the January 2018 issue of Tank Storage Magazine. It was written by Gavin Yuan, general manager of LBC Shanghai Shipping Terminal and Bruno Lhopiteau, managing director of Siveco. Click here to download the original article (English only).
LBC Shanghai Shipping is making tangible progress towards better risk prevention with the use of a specialised risk prevention management system.
In recent years, accidents in storage terminals have made headlines in China, prompting local authorities to strengthen regulations and to very significantly step up law enforcement.
The same trend can be observed across industries, as the Chinese government priorities sustainable development under its ‘China Dream’ campaign.
Numerous factory closures were reported in the second half of 2017. As plants were forcibly shut down after failing government inspections, many businesses, including multinationals, saw their supply chain impacted as a result. Strict regulations have actually been in place for years already, but authorities met difficulties enforcing them.
Today, better enforcement takes the form of more rigorous audits and by-the-book punishment if the company is found non-compliant. Considering the risk to get thrown in jail, general managers now treat these matters much more seriously than in the past. In the wake of the 19th Communist Party of China National Congress, this ultimately positive trend is set to continue.
When accidents or incidents occur, terminal operators face dire legal consequences (penalties, suspension of license, jail time), as well as impact on revenue, repair costs, insurance premiums, not to mention staff motivation, company image and stock value.
Recently, a number of locally-owned and operated storage terminals have been closed and their executives punished due to major accidents. Although no international terminal has been shut down due to safety issue, administrative mishaps with mandatory filings have led to temporary or partial loss of license by one international operator (this was not due to actual safety issue at the terminal).
Sometimes associated to wrongdoings, investigations have shown that incidents almost always stem from a lack of technical knowledge at both management and working levels: decisions made without understanding of their potential impact, tasks performed without following proper proce-dures and methodology. This grassroots challenge is the most difficult to address.
The comparatively late industrial development of the Chinese economy, compounded by the sheer size of the country and the extremely rapid growth experienced in the past decades, led to an acute shortage of experienced managers, engineers and skilled technicians, more particularly with the multi-disciplinary knowledge essential for maintenance. In such a market, hiring ‘the best people’ is not a viable option and the necessary training takes years.
At the same time, cutthroat competition leads Chinese terminals to apply low rates to secure business and to operate at times with very high throughput, resulting in excess fatigue for both the facilities and staff. Insufficient funding and time are allocated to maintenance. Such operating conditions contribute to more failures and accidents, to which the government inevitably reacts with stricter regulation. As observed in other markets, emphasis on regulation may unfortunately detract terminals from developing a sound maintenance program specific to their facilities.
BALANCING THE PROBLEM
In this context of increasing regulatory oversight and toughening market conditions, LBC Shanghai Shipping Terminal attempted to balance all aspects of this complex problem. At the end of 2016, the company, which operates a 74,200 m³ bulk liquid chemicals and petroleum products storage terminal in Shanghai’s Waigaoqiao area, launched a project with Siveco, a maintenance consultancy with a long experience of China, with the goal of setting up a risk prevention management system (with support from an specialised IT system) in line with the ISO 55000 Asset Management and ISO 31000 Risk Management standards.
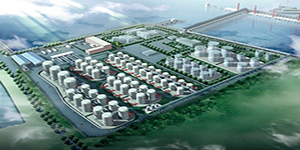
LBC Shanghai Shipping
The LBC Shanghai Shipping Terminal project makes use of two powerful tools backed by Chinese government campaigns:
In its drive to improve industrial practices, the Chinese government has since the late 1990s been promoting ‘informatisation’ initiatives that amount to using IT as a shortcut to best practices. Results have been watershed since the necessary industrial expertise is often lacking, resulting in computerisation for the sake of it.
Having said that, high technology has proven to be a powerful motivator for maintenance teams, which too often – and rightly so – feel undervalued. There is also a general understanding or belief that technology brings best practices, which can be used to drive organizational improvement projects under the guise of IT. Furthermore, high-tech is very well accepted by Chinese personnel, a generally young workforce, equipped with the latest personal computing gadgets.
In a most recent development, the ISO 55000 standard, popular in asset management circles in the west, has become a Chinese standard under the name of GB/T 33172. An exact translation of the original ISO equivalent, without any local adaptation, has become effective on May 1, 2017, demonstrating the commitment of the Chinese authorities towards world-class asset management.
While driven by international standards, the LBC Shanghai Shipping Terminal initiative took into account the characteristics of the Chinese industry, most notably the need to enforce methodologies and good working practices, from managers to technicians. Over a period of a several months, the project took the terminal management and technical team through all the steps of implementing a sustainable risk prevention management approach.
First of all, an ISO 55000-compliant process was established. The goal here was to make use of ISO 55000 as a framework for improvement rather than aiming at certification. Critical assets and inspections points were documented and labelled with QR-coded tags. Technical staffs were trained to use a mobile application named ‘bluebee®’, running on explosion-proof ATEX-certified Android phones. The app helps capture information from the field, such as incidents reported in a structured manner for systematic analysis, and enforce best practices, such as inspections or troubleshooting procedures. The app connects to a cloud-based risk management platform operated by Siveco, which contains all inspection routines, standard operating procedures and technical data. The platform produces regular analysis reports, as well as real-time graphical indicators showing the project’s progress, identifying risk areas, tracking the corrective and preventive actions taken.
With the app, scanning of QR codes, automatic time stamps and onsite photos prove that inspections are actually performed, in ways that a paper-based system with regular audits could never achieve. This is particularly true in China, generally considered a low-trust environment (‘how do we know for sure the job was done’, ‘who audits the auditors?’). Indeed, inspection forms (either preprinted or printed from a CMMS program), common in the industry, seldom accurately reflect the reality in the field: in China all checkboxes are invariably ticked off. CMMS relies on manual input after the fact, an unrewarding labor intensive task often relegated to clerks or interns, struggling to decipher the workers’ handwriting. Such systems fail to provide evidence that work has been done as defined, while offering no useful feedback for analysis and improvement.
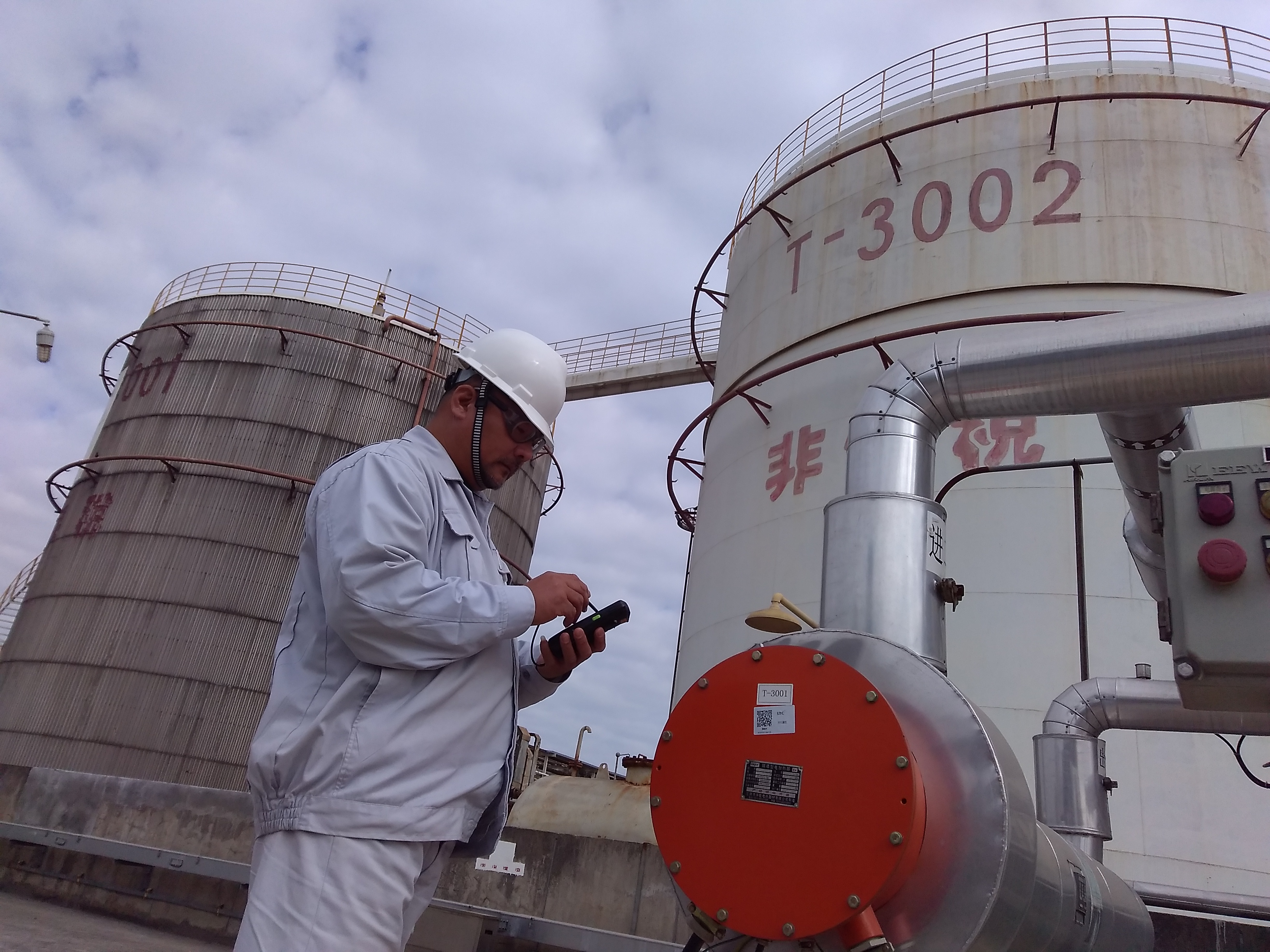
LBC Shanghai Shipping technician using bluebee®
Another key aspect of the system is that it enables training on-the-job, in addition to classroom training on related concepts and methodologies during the implementation phase. This ‘learning by doing’ approach has proven very effective in China in other projects conducted by Siveco and its efficacy over other forms of training is backed by scientific research.
Standard operating procedures (SOPs) have been designed, combining regulatory obligations, risk prevention ‘best practices’ and existing work practices: great attention was paid not to disrupt current operations by introducing totally new SOPs that would confuse technicians (a common pitfall for western operators in China). Instead, the goal is to continuously improve SOPs and preventive maintenance plans. On the mobile devices, inspection procedures appear with step-by-step actions, providing guidance to onsite personnel, especially for infrequent jobs.
In the app, some work actions may require scanning (for example scanning of a specific QR-coded inspection point), photos (mandatory or not depending on the task) and simple ‘smiley’ feedback (good, bad, requires follow-up, not done).
Designed for busy maintenance technicians, the app does not require any typing. When inputting meter readings or measurements, the ‘bluebee®’ app give immediate warning for off-range readings, prompting the technician to double-check his reading and/or initiate corrective actions. Some abnormal reading will also trigger automatic response in the back-office database, typically prompting condition-based maintenance work.
Any deviation between planned and actual work automatically generates exception reports for supervisors and managers to review.
In the storage industry, which is characterised as being generally conservative and traditional, the use of high-technology also plays a motivating role to unite the team around the common objective of improving risk prevention. Today, all departments of LBC Shanghai Shipping (HSE, operations, engineering, warehouse) use the system in their daily work to drive continuous improvement.
Getting rid of the old paper-based system and of the various Excel spreadsheets also meant that the corresponding administrative time could be reallocated to preventive activities. The overall workload may not have been reduced, but it shifted markedly from non-productive and corrective tasks towards risk prevention.
The Siveco system demonstrates its commitment to safety and compliance to all stakeholders, by showing full traceability of actions in a very visual, tangible manner (technicians using the app for all their tasks, managers showing real-time indicators on a display panel). By ensuring regulatory compliance, continuously educating personnel on-the-job and, at the same time, establishing a feedback loop to strengthen engineering practices the company aims to cut the Gordian knot that Chinese terminals have been facing.
With stiff challenges still ahead, the company believes that exchange of experience between terminals in China will promote further improvement in the industry and allow them to positively contribute to society as a whole.
Siveco has recently been recognised with a Chinese industry award for asset management informatisation.
About Tank Storage magazine
Tank Storage Magazine is the leading industry publication dedicated exclusively to the bulk liquid storage industry. It is read by terminal managers, senior engineers, logistics/distribution managers and CEOs within oil, gas and petrochemical facilities as well as third party terminal operators. Tank Storage Magazine is published by Easyfairs UK Ltd. Easyfairs deliver the world’s largest portfolio of tank storage events, which take place in key bulk liquid storage hubs around the globe. Tank Storage Magazine is the official publication for all events– StocExpo in Antwerp/Rotterdam, Tank World Expo in Dubai, Tank Storage Asia in Singapore, and Tank Storage Germany in Hamburg.