Results of the 2012-2013 “Maintenance in China” Survey
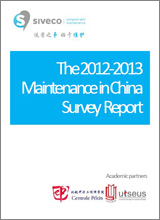
Executive Overview
This 2012-2013 Maintenance in China survey report provides a snapshot of the current maintenance management practices of industrial companies in China and of their improvement plans in the near future.
Results are summarised in this month’s Reliability article. Respondents will receive the full report, also available upon request.
Results are summarised in this month’s Reliability article. Respondents will receive the full report, also available upon request.
Respondents
The survey covered 1,569 respondents, 834 different companies, a total estimated 1,200 sites all over China.
55% are process manufacturers (mostly chemicals), 39% discrete manufacturers, 6% non-manufacturers.
The survey is dominated by mid-size (72%) international (84%) manufacturers.
The survey is dominated by mid-size (72%) international (84%) manufacturers.
Findings
Overall, the maintenance function tends to be under-budgeted and under-staffed in China compared to international benchmarks.
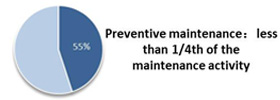
Results show low levels of preventive maintenance (less than 1/4th of the maintenance activity for 55% of respondents) with correspondingly low staffing in the maintenance engineering and planning function.
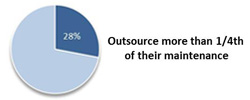
There is a significant increase in outsourcing compared to previous years (28% outsource more than 1/4th of their maintenance), with no observable impact on performance.
Respondents recognize the improvement potential, more particularly in terms of maintenance’s impact on operations and productivity (half of the respondents believe that 20% or more failures could be prevented, 46% think preventive maintenance could have a large – over 10% – impact on productivity).

Companies however lack the necessary skills, decision support and management tools (56% have no adequate computerized tool, 30% cannot track production losses due to breakdowns, only 22% track failures of all their equipment, only 30% have regular analysis meetings). This partly explains the very significant discrepancies in answers observed between respondents from the same company.
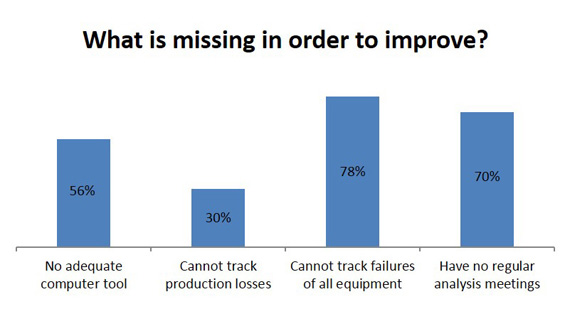
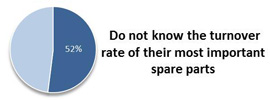
Spare parts represent another under-optimized area (more than half surveyed companies do not know the turnover rate of their most important parts), often not covered by corporate productivity improvement programs.
70% of respondents indicate they will pay more attention to maintenance: 63% envision internal activities to improve maintenance, 52% external actions (training, consulting). 52% are considering the implementation of computerized-based tools, a figure significantly higher than in previous years.
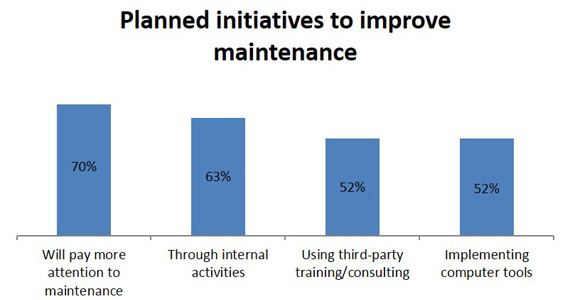
Overall there is little change from previous years’ results, apart from the increase in outsourcing, the growing interest in computerized tools and perhaps a better awareness of maintenance issues.
Conclusion
Maintenance remains vastly under-optimized in China, which presents a significant risk for manufacturers, in a context of slowing investments, existing facilities showing the effect of aging (often faster than expected due to construction issues and lack of preventive care) and growing skills shortages.
There is however an increasing awareness of the issue, with a clear need for management tools and for support currently not offered by corporate programs (WCM, ERP). Positive impact is expected from maintenance improvement initiatives, in terms of productivity and risk avoidance.
In 2013, maintenance improvement represents a new priority for manufacturers in China and a “low-hanging fruit” with good ROI potential.
Click to read online or download the full report.