The Future of Operation & Maintenance
This article was previously published in the June 2021 issue of APUEA magazine.
Media hype has led us to believe that technology would soon revolutionize maintenance. Dreams of flying robots, video game-like smart glasses, flashing digital twins, often hold the sad promise of getting rid of maintenance people altogether. The reality remains that the more automated, the more sophisticated the systems, the more demands are put on maintenance people and their skills. The problem is compounded when this glorious technology did not address actual needs.
Predictive maintenance is often said to be the low hanging fruit of Industry 4.0. Yet to maintenance practitioners it is nothing new. Technology has improved, but the implementation challenges we met in the 1990s still exist today: a maintenance strategy that utilized predictive maintenance must be defined, relevant measurement points and corresponding actions established, people trained.
The idea to use 3D BIM models in operation has also emerged. We have all seen movies showing a technician using a tablet to view “behind the walls”, almost knocking his head on the pipes, breaking half a dozen safety rules in the process of demonstrating this unnecessary usage of BIM. Luckily, this seldom passes the Proof-of-Concept stage. The company could not afford all the broken iPads.
The Covid-19 pandemic has seen many large companies slashing their innovation budgets, while paying lip service to the transformative nature of innovation in times of crisis. Yet, it has also accelerated certain trends. The use of smart glasses for remote support is perhaps the most striking example, paralleling the growth of video conferencing apps. In fact, this usage of “smart” glasses is often nothing more than portable, head-mounted, video conferencing…
Once at a conference, we were shown a fantastic 3D application combining all promises into one. Operators could navigate a hyper-realistic plant model, walk to the location of a meter, view the current meter value (capture from the SCADA), before walking to the next point. This was billed as a virtual meter-reading solution. Most people in the room were very impressed by this beautiful demo of how an otherwise perfectly functional engineer could waste his time walking around a 3D model (at approximately the same speed as in the real world) when a traditional SCADA could do a much better job, displaying in the control room all the meter values, or – here is the real improvement – only displaying abnormal readings on a simple plant or process layout. Whatever happened to common sense?
No amount of in-house and vendor-awarded innovation trophies can change the reality: this is not the future of Operation & Maintenance!
The main challenge of O&M is not its lack of efficiency, as technologists seem to believe. Instead, it is to address strategic needs, O&M risks, compliance. And doing so efficiently, of course. One of our strategic needs is also to enable workers with limited skills to deal with increasing sophisticated assets, in an increasingly complicated, regulated, risky world. Most of the tech touted by vendors and consultants ignores all that.
Standards such as ISO 55000 Asset Management, itself closely related to ISO 31000 Risk Management, offer a useful framework to address this need. I recommend its practical usage as guideline for the design and implementation of O&M technologies that make sense for your business. This naturally leads to redesigning most of the examples given above, as we have done at Siveco China with our clients all over Asia. As a result, the O&M technician takes the central place in the smart project. His role is promoted, his skills enhanced, his motivation increased.
Real experience
Global automotive and industrial supplier Schaeffler has embedded Siveco China’s Smart O&M technologies in its SmartLink condition monitoring solution, and vice-versa: SmartLink is also directly accessible from the bluebee® app “for the worker of tomorrow”, enabling the engineers to drill down to specific measurements and vibration profile to support their analysis. All information can be seen in context: failure history, past diagnosis, next maintenance visit, trends for a better decision.
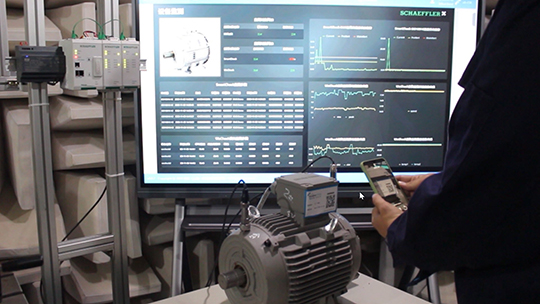
In the Sanwai Sewage Treatment Works project in Hong Kong, Siveco China ensured handover of technical data from construction to maintenance through the implementation of its BIM for Asset Management solution. Once the plant started operation, the O&M team uses the Siveco China suite for their daily work, which provides easy navigation into complex technical data, including when needed to the BIM model itself, for example to establish safety procedures or coordinate complex work with contractors. Altogether the system forms a true Lifecycle Digital Twin.
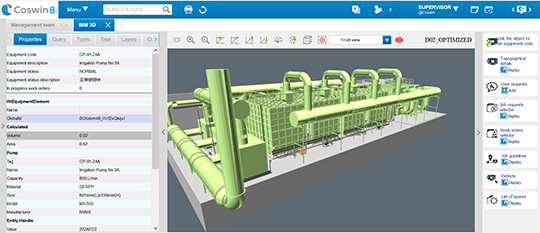
Hong Kong Airport Authority has taken the Smart Glass beyond glorified videoconferencing, to conduct the inspection of critical assets using the bluebee® mobile app plugin for smart glasses, with the objectives of providing a hands-free, convenient and safe wearable device for O&M technicians, while standardizing the technical inspection process. Technicians view step-by-step work instructions, interact with the app using voice commands and hand gestures, record their work as required.
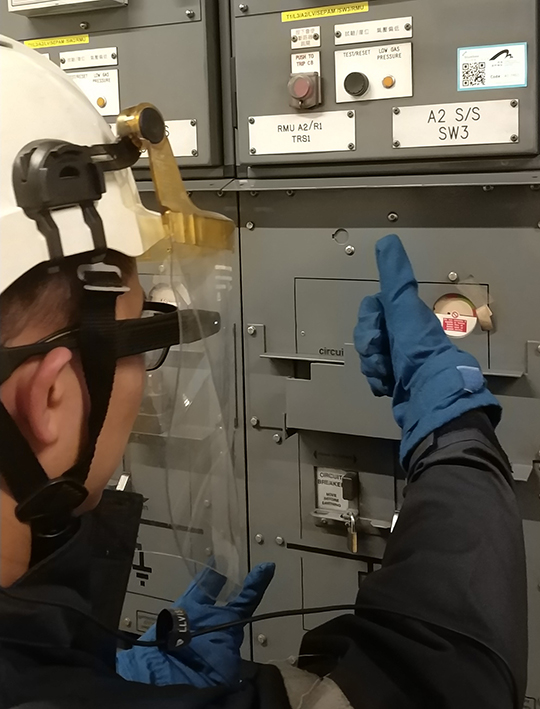
Organica, a provider of innovative wastewater treatment solutions, also supports O&M teams with highly practical, non-nonsense, Digital Twin solutions based on proven technology. The solution integrates the plant’s 3D BIM model and real-time data from the SCADA, both designed by Organica, into Siveco China’s Smart O&M platform. Relevant SCADA values are shown in the mobile, together with related maintenance instructions, for the technicians in the field.
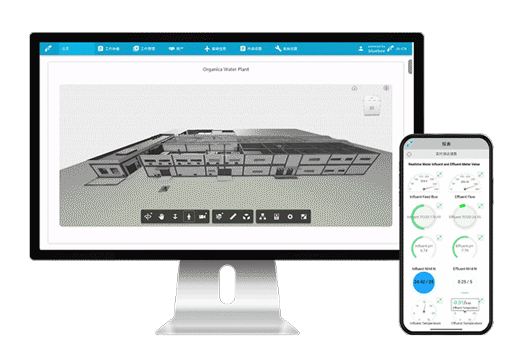