Implementing “5 Whys and 1 How” in Coswin 8i
As part of their WCM, Lean or TPM approach, some of our customers follow the 5W+1H (“5 Whys and 1 How”) process, or similar methodologies, to help identify the root causes of failures. This process can be supported, and all related information recorded, in a tab of the Coswin work order, to ensure the process is systematically followed and to allow systematic analysis of failures. Here we will show how use the Coswin 8i Resource Editor and Free Modules tools to realize the requirement in Coswin 8i. The same can also be achieved with bluebee® (not described in this article).
The Coswin 8i tools
Coswin users are already familiar with the Resource Editor, which allows easy screen customization. This tool is used in every Coswin project to change field labels (e.g. a “Hazard Report” may become a “Corrective Action Request” or whatever term is commonly used by users), to add color codes (e.g. urgent work orders will be highlighted in red) and to simplify screen layouts (e.g. operation users may only see very simple work order form, while maintenance users will see all of it).

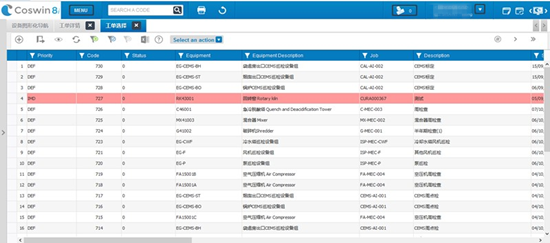
Most customers however do not imagine the almost limitless possibilities offered to adjust Coswin 8i almost beyond recognition, to comply with special requirements or meet unique interfacing needs, without any programming. This is achieved by a combination of Coswin tools: the Resource Editor, the Diagram Editor, the Free Modules, as well as interfacing tools, external programs and plug-ins. This article sticks to the most basic tools, with a focus on the Free Modules – which most Coswin users have in fact never heard of…
Some of the Coswin 8i tools were featured in this previous newsletter article (https://newsletter.bluebeecloud.com/en/Coswin-tips-tricks/Coswin_tips_tricks-personalisation_tools/).
The Free Modules
“Are they really free?” is the first question you may want to ask… As confusing as the name may be, it simply refers to a large number of modules without pre-identified usage, containing screens and fields without labels, which can then be fully configured using the Resource Editor. Those data fields can be populated using the Clic-Clac migration engine and can be accessed by Coswin Reports, just like any other Coswin data. They are simply available as a standard feature of Coswin, although you may not see them with your current end-user access rights.
“What can we do with it?” Your imagination is the limit, as far as common project situations are concerned. This section will try to show you examples of how we have used it in projects.
Example: 5 Whys and 1 How
1. First of all, we create the 5W+1H tab in the resource editor.
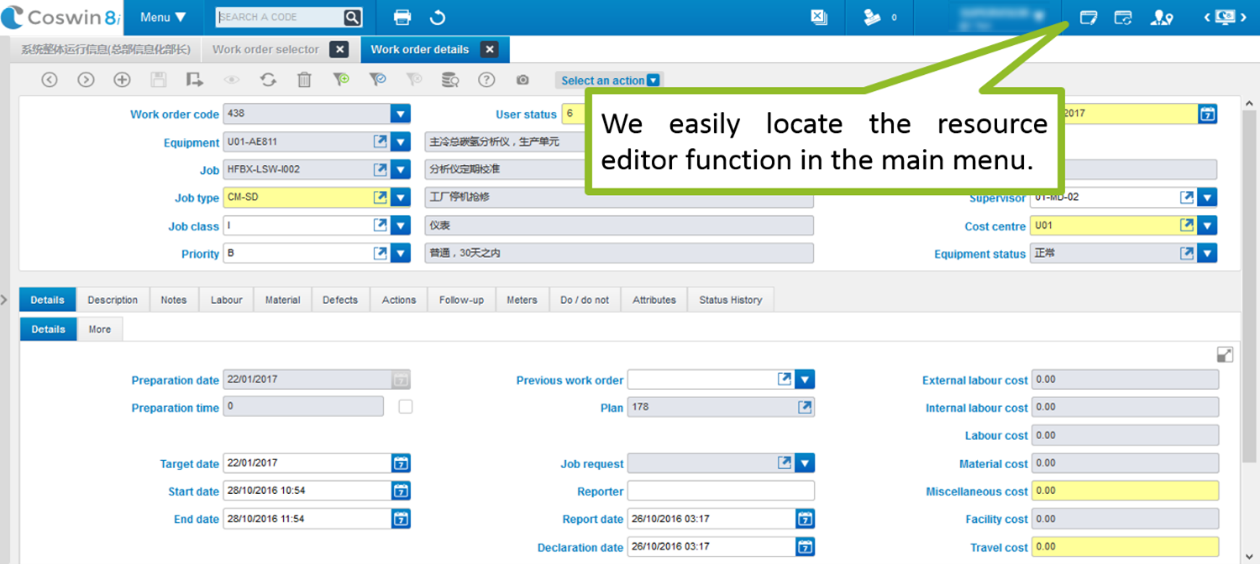
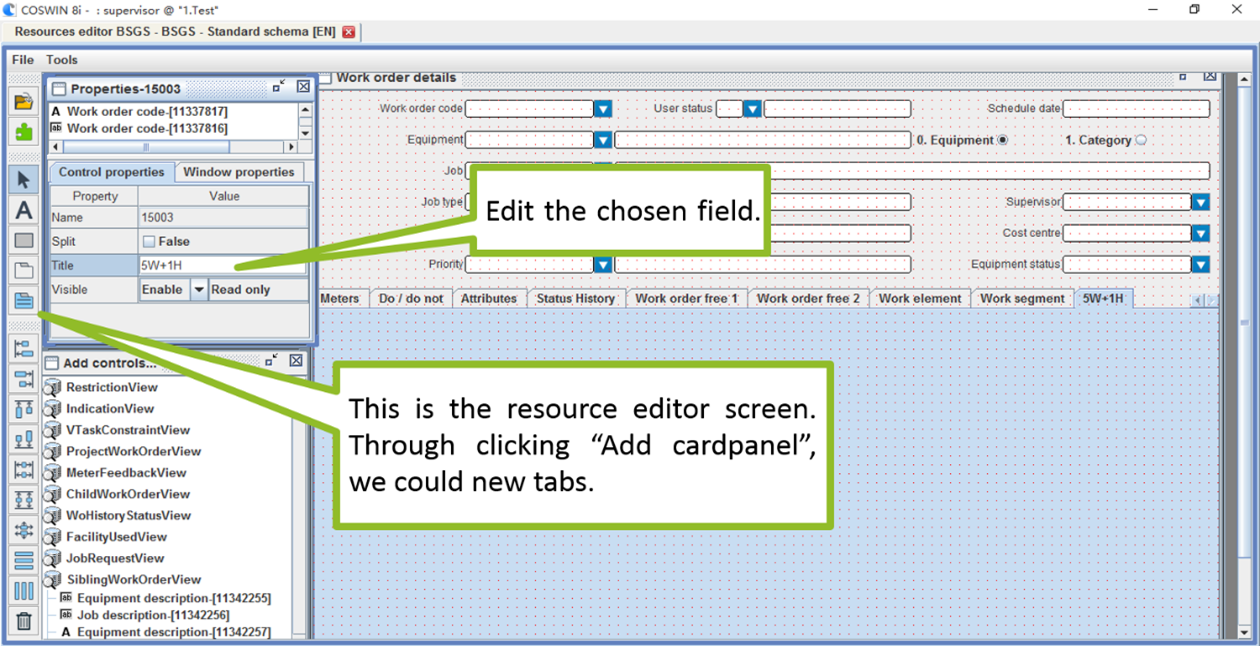
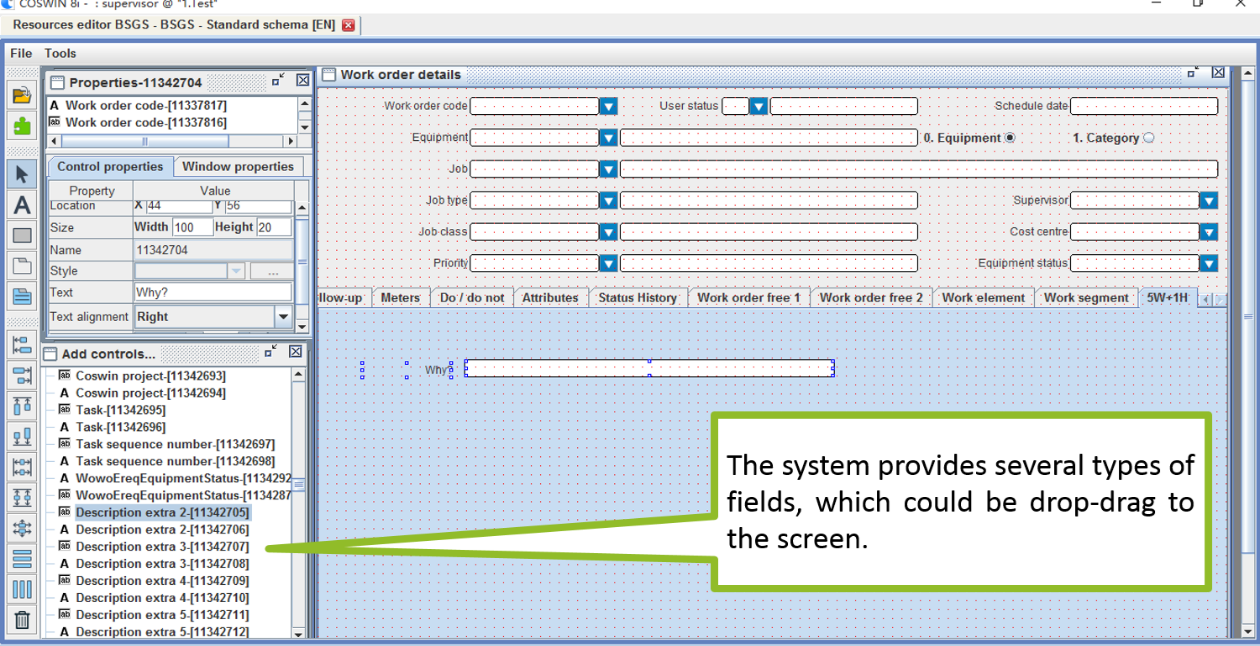
2. Then we are able to design our own 5W+1H page.
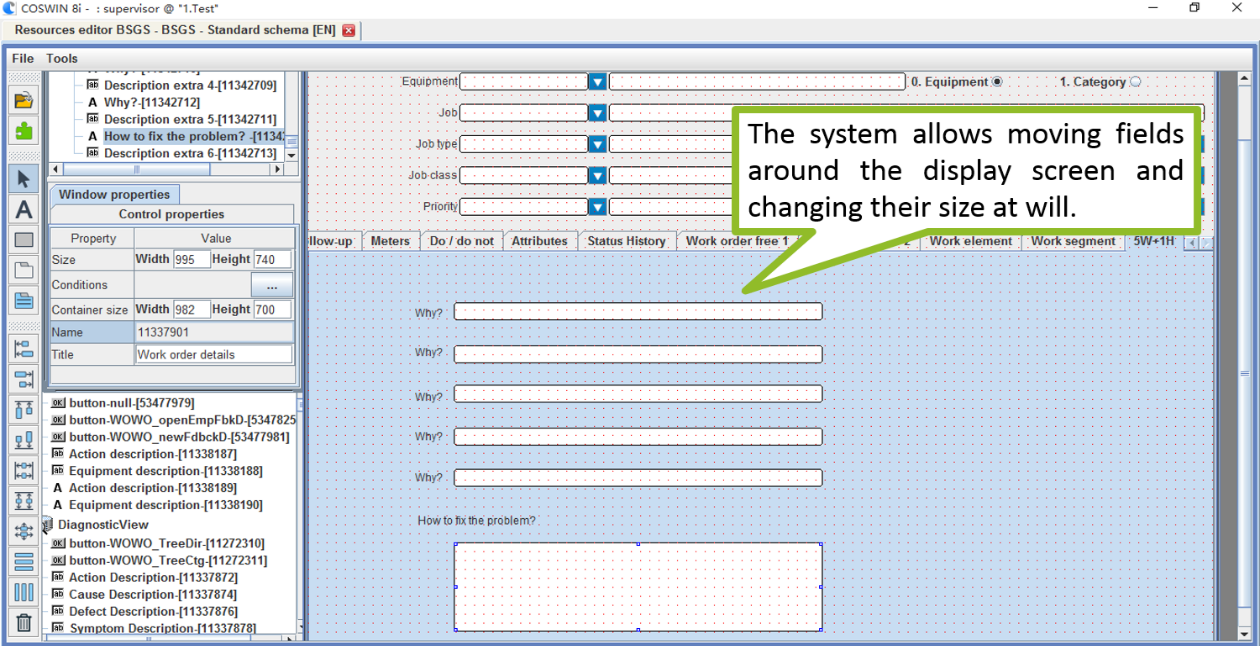
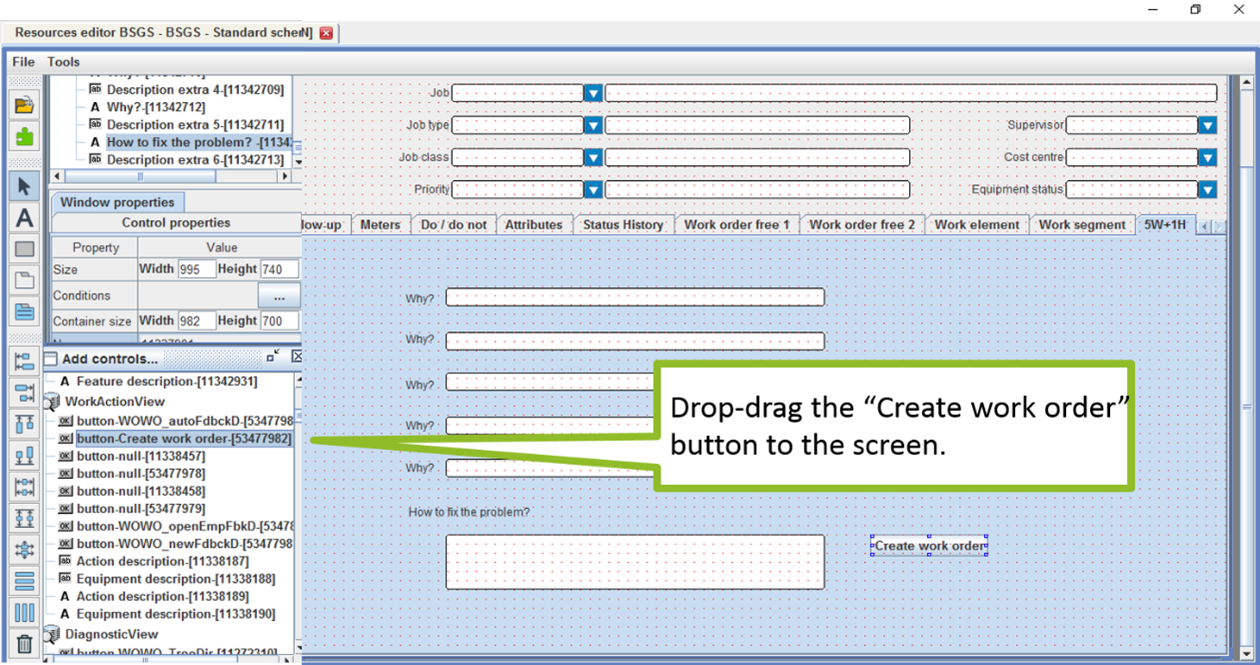
3. Finally, we can now see the free module on the WO screen, and it is possible to operate on it.
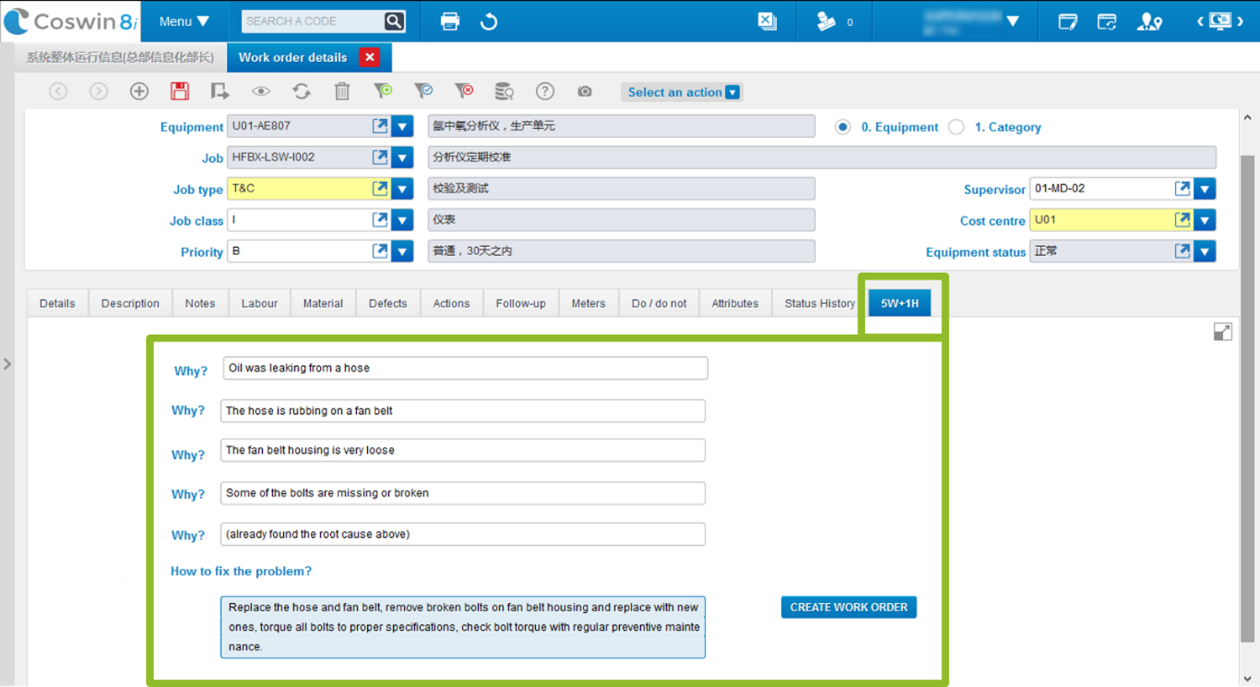
Systematic analysis
While the 5W+1H tab in the Work Order ensures workers follow a structured methodology, the data is accumulated in the central database of Coswin 8i, thus allowing systematic analysis for improvement purposes. This is achieved with the embedded reporting tool of Coswin 8i
TPM or WCM reports are however notoriously difficult to obtain from traditional IT or ERP systems, as they involve complex data from multiple sources. One of our large automotive client for example could never extract such report from their multi-million dollar integrated ERP system, in spite of many efforts trying to develop such reports. With Siveco’s Smart Maintenance solution, the report is immediately available for analysis and decision support:

PM Machine Ledger
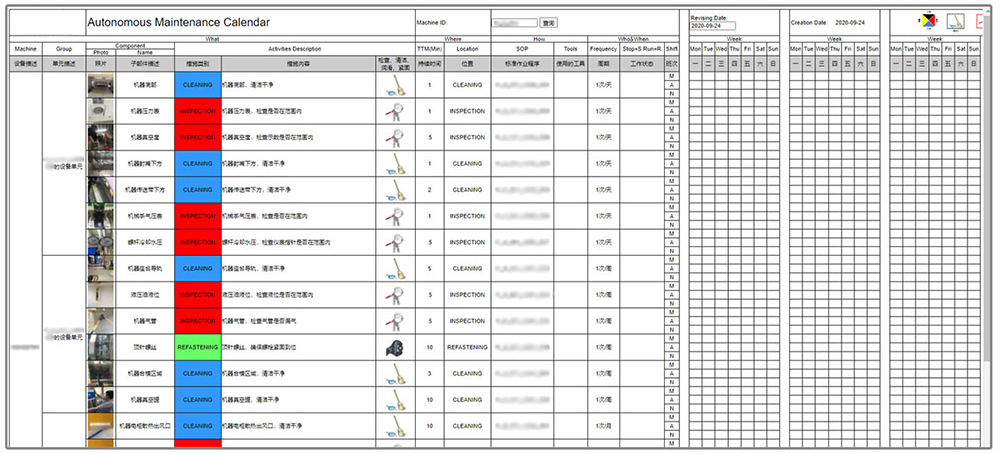
Autonomous Maintenance Calendar
Other special requirements?
Apart from 5W+1H and similar processes, customers operating in very specific industries may have requirements to record data that do not exist in a standard CMMS, due to their specific processes or government regulations, certifications and standards. In 99% of the cases, the requirements are not functional: they involve adding new data fields, creating new screens or changing existing screen layout. They can be realized with Coswin 8i!
For example this customer case study from Baosteel Gases talks about the RCA (Root Cause Analysis) and FMEA (Failure Modes and Effect Analysis) processes in Coswin 8i and bluebee®, achieved in the same manner: https://newsletter.bluebeecloud.com/en/customer-story/digitalizing-om-management-at-baosteel-gases-plants-with-emm-and-bluebee/
For example this reliability article takes the FMECA management module built into the Baosteel Gases EMM system (Coswin 8i) as an example to introduce the application of FMECA in the actual enterprise quality management system in detail: https://newsletter.bluebeecloud.com/en/reliability/integrating-fmeca-in-your-maintenance-system/